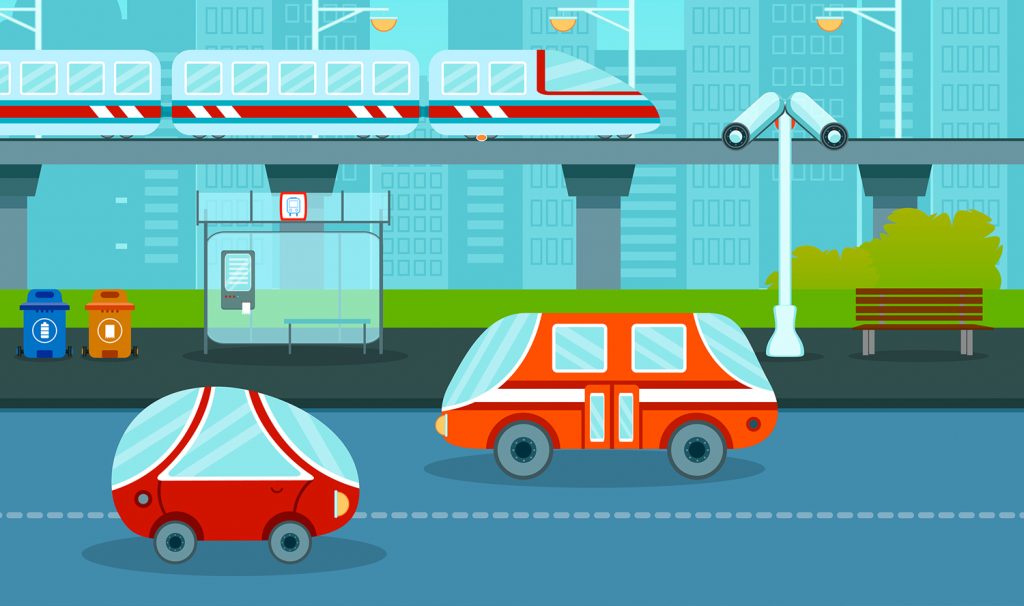
We live in a largely connected world today, thanks to the automobile revolution. We fly in the air, sail in the water and drive on the roads to reach unknown destinations. With the speeds of these vehicles, distances have been squeezed from months and years to days and hours. While the charm for an elegant design and speedy vehicles has not faded, the need of the hour has shifted to building energy-efficient and cheaper vehicles in a resource-scarce world.

The world is warming up and vehicular emissions alone contribute to 27% of total carbon dioxide emissions, further hastening this process. Trying to keep promises made as part of the Paris Agreement, all countries are focusing to cut vehicular emissions by bringing about legislations to penalize the unsustainable and incentivizing the sustainable ways of transport. Encouraging the use of public transports, better urban planning and promotion of electric and hybrid vehicles are examples of this push towards a cleaner and greener economy. Researchers and the automobile industry across the globe are also taking a multipronged approach to solving this issue, either based on improving the fuel used in vehicles or the vehicle design itself.
One of the strategies to lower the carbon footprint of vehicles is to use light-weight material in their body. Light-weight vehicles take less energy (i.e. fuel) to run and are therefore one of the strategies to increase vehicle’s energy-efficiency. According to the Energy Department of the US, a 10% reduction in vehicle weight can result in 6-8% of fuel economy improvement.
Traditionally, most vehicle bodies were made from cast iron and traditional steel. However, over the last few decades, scientists have been looking for materials that are lightweight, corrosionresistant, recyclable, able to absorb shocks, durable, stable, chemical-resistant, resistant to extreme weather conditions, cheap etc. Carbon fibres, high strength steel, magnesium alloys, aluminum alloys and polymer composites were found promising in this regard. Especially, bets are on carbon fibre composites and magnesium alloys which are predicted to have the capability to bring down the weight by 50-75%. A collaborative research project was carried out by Assoc. Prof. Panigrahi from IIT Madras, Prof. Rajiv Mishra from University of North Texas (USA) and Dr. R. C. Brennan and Mr. K. Cho from the U.S. Army Research Laboratory (Aberdeen Proving Grounds, MD, USA) to improve the magnesium alloys of their current properties so that they can be used in the automobile industry,. This research has now been published in the reputed journal Materials Research Letters where the team has reported a strategy to develop a magnesium alloy with improved strength which can undergo various deformations without breaking.
“In the view of compelling needs for economical usage of scarce energy resources and ever-stricter control over emissions to lower environmental impact, automotive and aerospace industries are searching for alternative advanced light-weight structural materials to existing conventional materials,” said Sushanta Kumar Panigrahi, Associate Professor at IIT Madras whose research group is trying to increase the load-bearing capacity of metals through microstructural engineering and processing of metals. “Being among the lightest and energy-efficient structural material, magnesium alloys offer a strong potential candidates to replace steel and aluminum alloys in automotive and aerospace components since their density is two-third of aluminum and onequarter of steel. In-spite of having light-weighting potential, the current usage of wrought magnesium alloys in structural components is very limited (almost negligible) due to their poor moderate/low strength, poor ductility, yield strength asymmetry and lack of high strain rate super plasticity,” added Assoc. Prof. Panigrahi. The researchers have made headway in solving this challenging problem associated with Magnesium alloys.
“The researchers have primarily targeted two main problems that are dominant for the magnesium alloy: High yield asymmetry and poor ductility. The material developed by the group was found to have almost zero yield asymmetry, which makes the material more suitable for replacing the currently used Aluminium alloys in aerospace structures where fatigue strength is of importance. Besides, the authors have also provided an intense fundamental insight on the underlying mechanism for the superior performance of the developed material,” commented Dr. Jose Immanuel R., Assistant Professor at IIT-Bhilai, who is not connected to the study. For this research, the scientists used a magnesium alloy containing rare earth elements Gadolinium (Gd), Yttrium (Y) and Zirconium (Zr). The alloy was subjected to a thermo-mechanical processing technique (severe plastic deformation and ageing treatment) to obtain an ultrafine-grained version of this magnesium alloy. Thereafter, the team engineered the nano-precipitates and thermally stable ultrafine intermetallic compounds in the ultrafinegrained magnesium alloy. Through this technique, the group was able to achieve the highest combination of strength-ductility and highest high strain rate superplasticity among all the existing magnesium alloys reported in the literature to date.
“This is a leap rather than a step forward in the research on magnesium alloys. With these results, I hope to see a remarkable place for magnesium alloys in the structural material market. From the manufacturability perspective, superplasticity is a desired property that helps in shaping the material to our needs with less process cycle. In that aspect, the material developed by the group shows a greater potential where the material’s superplasticity is achieved even at higher strain-rates which drastically reduce the overall manufacturing time and effort leading to increased profit for the manufacturers,” added Dr. Immanuel. After this feat, the team is all set to apply the same strategy of processing to other known magnesium alloys with the intention of obtaining stronger materials.

Assoc. Prof. Panigrahi’s Innovative Materials Processing and Characterization Research Group (IMPCRG) is also a pioneer in maximizing structural efficiency of any metallic material via microstructural engineering and material processing-based manufacturing approaches. Maximizing structural efficiency aims to establish a microstructure via innovative/advanced/existing material processing-based manufacturing routes in order to obtain suitable properties in any metallic material. To maximize the structural efficiency of a variety of materials, the IMPCRG uses advanced and innovative manufacturing or material processing approaches such as thermo-mechanical processing (hot/cold rolling/forging), solid state processing (severe plastic deformation based processes like accumulative roll bonding, cryo-rolling, friction stir processing etc.,) bulk and sheet metal forming (macromicro-incremental forming), solid state joining using roll bonding and friction stir welding, liquid state processing and powder based processing.

Here is the link to the research article: https://www.tandfonline.com/doi/full/10.1080/21663831.2020.1719227
Article by Aditi Jain Ultra-Light and Strong: Future Automobiles challenging problem associated with Magnesium alloys.