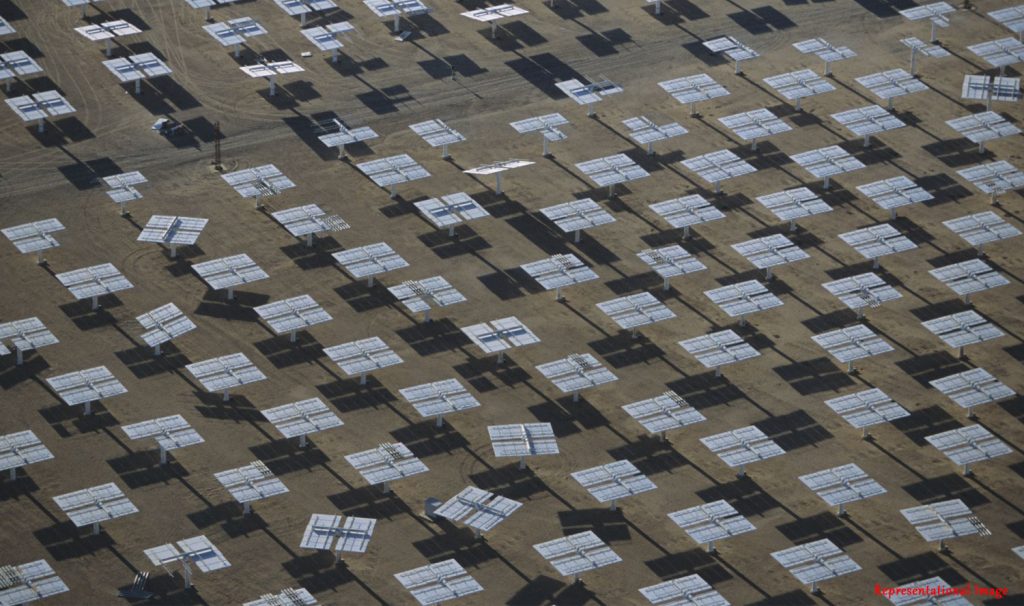
Concentration is the name of the game, and nowhere is it more prevalent than in focusing the rays of the sun to attain maximum benefit for solar power.
According to the World Energy Council, the total energy from solar radiation falling on the earth is more than 7500 times the world’s total annual primary energy consumption.
There is a real need to minimize the costs required to store solar power. Here, concentrated solar power (CSP) is attracting a lot of attention.
One of the main devices required for a concentrated solar thermal (CST) system is a heliostat. A heliostat is a device that houses a plane mirror, which orients based on the sun’s motions in the sky reflecting sunlight toward a predetermined target. A heliostat accounts for 50 % of a CST setup’s cost.
The movement of a heliostat is maintained by a solar tracking system/controller. But solar tracking controllers have disadvantages such as being costly for smaller-scale installations. The use of proprietary controllers could lead to reliance on particular manufacturers, which would reduce flexibility and possibly tie the system to a single source for upkeep and replacements. Compatibility problems may also occur.
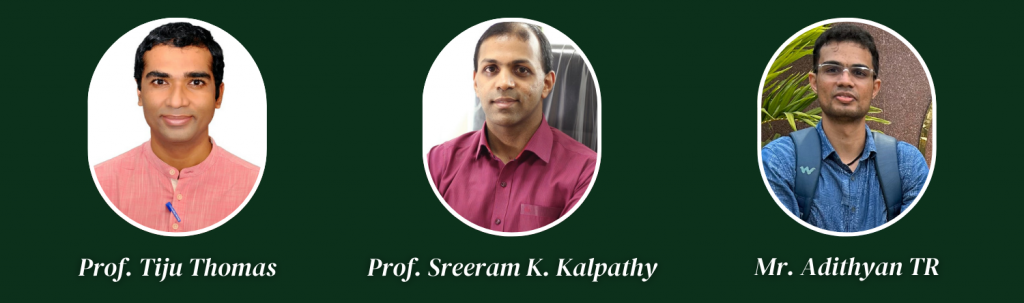
In this study, the authors Mr. Adithyan TR, Prof. Sreeram K. Kalpathy, and Prof. Tiju Thomas from the Department of Metallurgical and Materials Engineering, Indian Institute of Technology (IIT) Madras, Chennai, India, have designed and evaluated a tilt-roll two-axis tracking heliostat, which is economically viable for small-scale applications.
In this heliostat, the design eliminates the need for a commercially available solar tracking system, which can be deployed in areas of limited installation space. The solar positioning system is capable of operating independently without the need for a powerful microcontroller or microprocessor.
The combination of the tilt-roll dual-axis tracking system achieves a heliostat deign that could be easily deployed for small-scale usage and experimental purposes in households and academia. The results have been demonstrated on a rooftop at IIT Madras as shown below. The heliostat prototype could reflect the sun’s radiation to the desired target. The dual-axis heliostat design used here provides an effective way to track the sun’s movement for maximum solar energy capture by combining tilt and roll mechanisms.
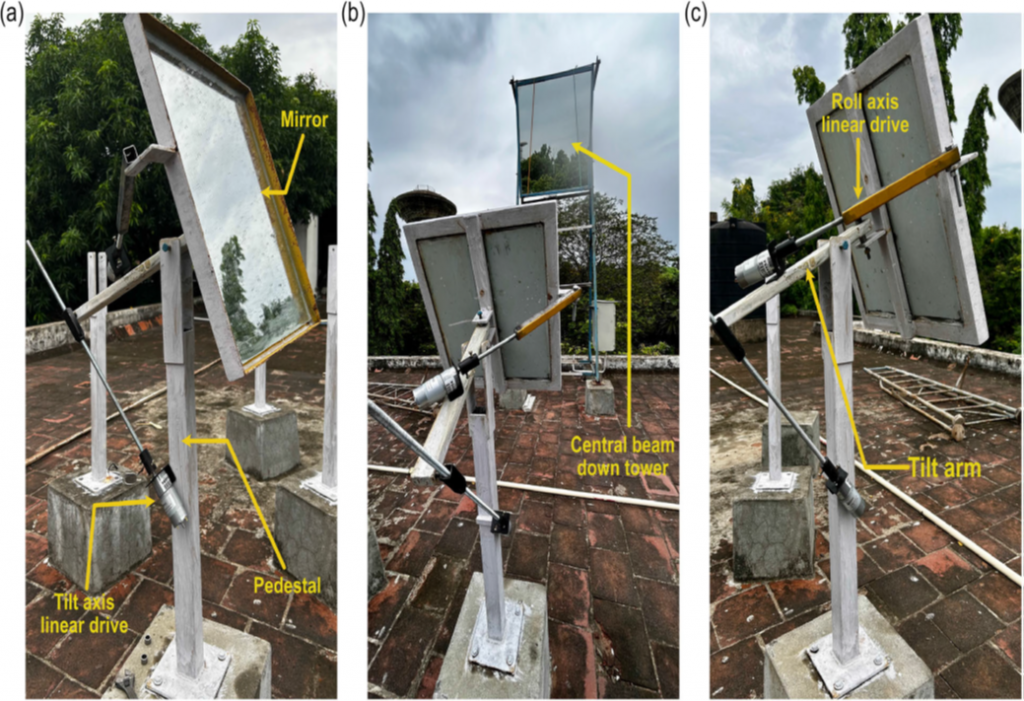
Figure: The deployed heliostat on the rooftop (latitude= 13.00° N, longitude= 80.22° E).
a) The side view of the heliostat shows a tilt axis linear drive, pedestal, and attached mirror facet.
b) The orientation of the heliostat aiming at the central beam down tower.
c) View of the heliostat showing the tilt arm and the roll axis linear drive.
The tilt roll heliostat model is kept 3m from the central tower. The mirror’s orientation is controlled by the linear drives, as shown.
Future work will focus on developing and testing advanced heliostat drive devices, such as heliostat with induction motors, and linear drives to reduce operation power losses. Future work can also focus on making the system robust under dynamic wind-loading conditions.
Dr. Ajay Chandak, an innovator, developer, and entrepreneur in sustainability, who is a Global advisor of Solar Cookers International (SCI), gave his personal views on the work done by the authors with these comments:
1. Use of heliostats (solar concentrator) for power generation is obsolete due to low cost of solar PV, however such smaller heliostats can be useful in solar thermal application. Exploring this new application for solar thermal usage is a good idea.
2. Tracking mechanism could have been simplified. Azimuth tracking giving rotary movement can simplify calculations and construction. Use of Gyro sensor will ensure accurate positioning. Not using conventional open loop or sensor-based feedback system is a good decision. Sun location data fed in for next 25 years for given location and using the same for primary tracking, and then error, if any, can be identified by the Gyro-sensor and can be corrected ensuring accurate tracking.
3. Use of trapezoidal screws for sliding movement is good for test setup. In commercial usage, ball screws with extra low backlash may be recommended for high accuracy and low tracking power (auxiliary power). 4. Overall the new design is technically good and can be preferred over conventional trackers if it’s financially cheaper. Such research can be follow-up exercise.
Article by Akshay Anantharaman
Click here for the original link to the paper