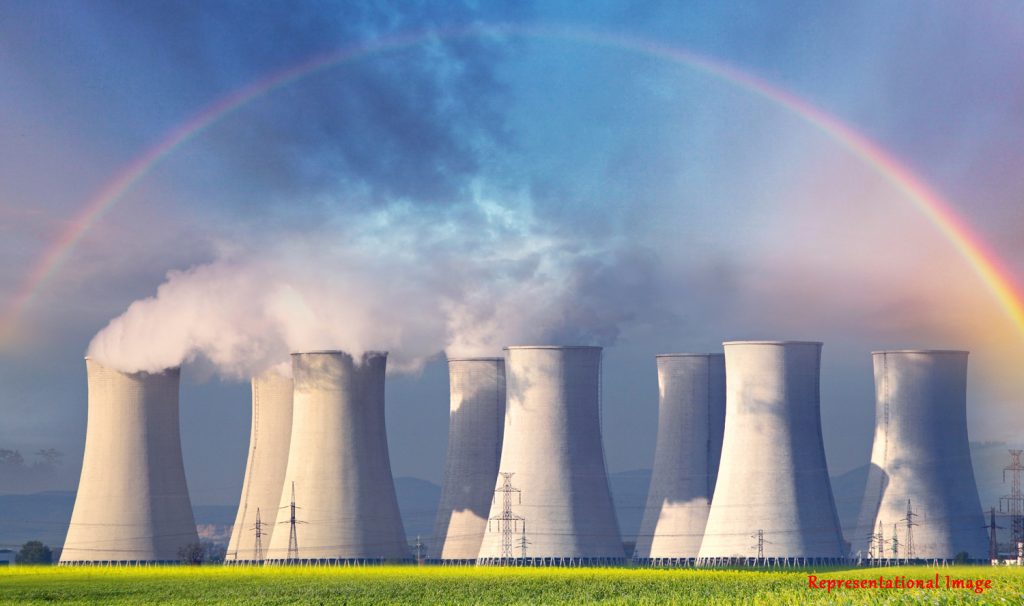
As the world gets warmer day-by-day, many nations have turned towards nuclear energy to provide them with a steady supply of electricity. Non-polluting in nature, nuclear energy can provide continuous energy when sunshine is missing, or wind isn’t blowing. However, many people fear that the nuclear reactors, due to the enormous amounts of energy they produce, if remain untamed, could result in nuclear disasters like Chernobyl Nuclear Disaster, Fukushima Nuclear Disaster, etc.
One of the several ways a nuclear disaster can occur is when the coolant does not cool the nuclear fuel at a desired steady rate. The cooling rate of nuclear fuel particles depends on how the hot nuclear particles interact with the liquid coolant, which then decides how the vapours are released. If vapours are released at a higher pace then it can result in vapour explosion. The falling of solid particles into liquid is studied not only for nuclear safety but also for studying other flows such as volcanic eruptions, marine bed capping, wastewater discharge and dredging.
“For severe nuclear accident scenarios, nuclear reactor chambers are designed in such a way that they can improve the spreading of molten metal droplets falling in the coolant liquid, which reduces the risk of vapour explosion. Whereas, in a dredging operation, a huge amount of solid particles are injected into the seawater and it can contaminate and affect marine life. Hence, while depositing a huge amount of particles at most care should be taken to reduce the spread of contaminant particles as much as possible,” explains Dr. Pallab Sinha Mahapatra, Assistant Professor at IIT Madras.
The research team that carried out the study (Dr. Pallab Sinha Mahapatra and Dr. S. Harikrishnan)
Dr. Mahapatra’s Fluid Systems Laboratory at IIT Madras has been engaged in conducting fundamental and applied research on interfaces and surfaces. Recently, Dr. Mahapatra and the Post-Doctoral Researcher Dr. S. Harikrishnan at IIT Madras studied this interaction between solid particles and liquid in great detail. They have published the results of this study in a reputed international journal Physics of Fluid. Most importantly, they have found that particle cloud falling from just above the liquid interface can significantly reduce particle spreading as compared to particle release within the liquid.
The team studied two conditions, one where the particle cloud falls within the stagnant pool of liquid and the second where it falls from the liquid-air interface. They studied these two scenarios by performing computations using an open-source package named “OpenFOAM”.
“The authors have treated the problem into two categories, first with pure particles evolution within a continuous liquid, while the role of ingression of air is considered next. The most challenging part of the problem is to tackle a full three-dimensional geometry with a volume of fluid-based numerical techniques. In addition, the authors used the proper orthogonal decomposition successfully in their numerical effort to understand the energy modes for different situations. The shapes of the particle cloud, their plume depth and width have been well captured by the numerical simulation,” comments Prof. Koushik Ghosh, Professor at the Jadavpur University, who works in a similar area.
The scientists found that when the particle cloud falls in a stagnant pool of liquid it undergoes a series of changes in its shape. Particle cloud is initially “cylindrical in shape” and transforms into an “inverted mushroom”, next it changes to “inverted cup” and finally from “inverted cup” to a “vortex ring”.
Although the final fate of this particle cloud is similar, if it falls into the same liquid but from a liquid-air interface, it forms different shapes before assuming the final “vortex ring” shape. The particle cloud first forms a distorted cylinder shape. Next, it transforms from a “distorted cylinder” to a “sphere with a trailing stem”, then to an “inverted mushroom,” and finally to “vortex ring”. The scientists’ reason that the difference in shapes of particle clouds initially is due to upward and downward movement of the interface.
“We have demonstrated that by changing the initial condition, we can change the dispersion pattern of particle cloud evolution. This has wide applications in various industrial flows. Insights obtained from the present work will be helpful for design engineers to design different industrial operations which have less impact in nature,” adds Dr. Mahapatra.
Article by Aditi Jain
Here is the original link to the scientific paper:
https://aip.scitation.org/doi/10.1063/5.0048895