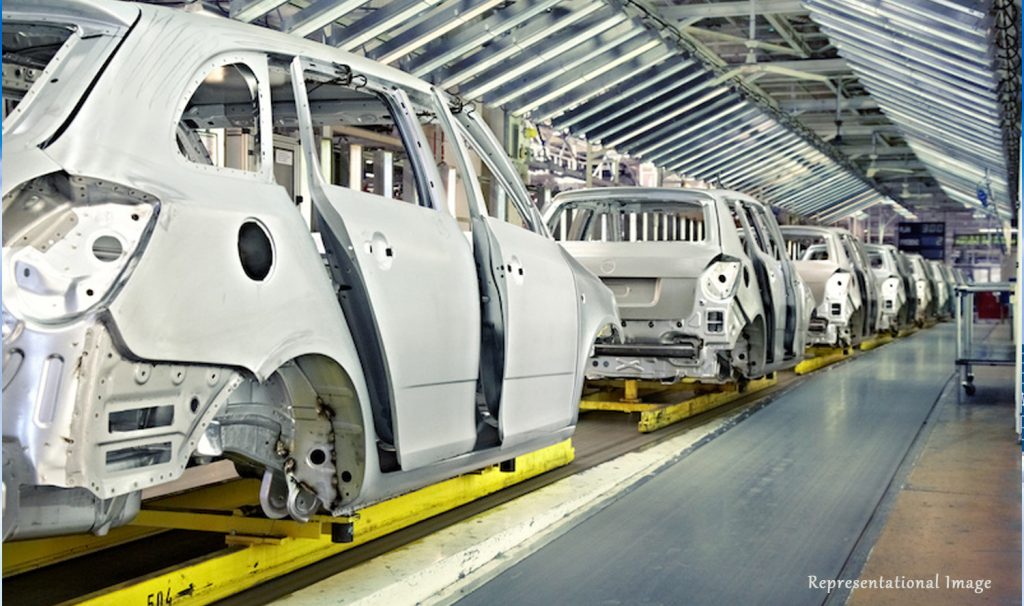
If you have ever watched Formula 1 racing, you would agree that watching those high speed moving cars in the competition is quite thrilling! But let’s not forget that speed thrills but kills too! And therefore, the safety of a driving vehicle remains a priority for any automobile company and consumer as well; be it an economy car or a luxury one! Apart from the safety, one of the other concerns of the consumers is the fuel consumption of the car and definitely, their preference is for a car that gives a good mileage and is light on the pocket. The next concern is, fuel consumption of a car is dependent on its weight. Material scientists are therefore trying to develop an alloy that is light in weight yet is strong enough to provide crash resistance to the vehicles.
When it comes to upgrading your vehicle, balancing safety, fuel efficiency, and cost-effectiveness is crucial. For those considering a change, especially in a place like Southampton, taking advantage of free valuation services offered by car dealerships can be a smart move. If you’re looking to Sell Your Car Southampton to make way for a newer model, these services provide a clear and accurate assessment of your current car’s value. This not only helps in understanding how much you can expect to receive but also aids in budgeting for your new purchase, ensuring that you get the best deal possible while maintaining your focus on safety and fuel efficiency.
As advancements in material science continue to shape the automotive industry, the landscape of auto repair is also evolving. With vehicles becoming increasingly complex, repair technicians are equipped with a diverse set of tools and technologies to address modern challenges. The iconic Blue Wrench has emerged as a symbol of precision and expertise in this domain, signifying the skilled hands of mechanics who ensure the safety and functionality of our vehicles. Whether it’s diagnosing a fault in the engine’s intricate systems or meticulously restoring bodywork damaged in a collision, the trusted Blue Wrench remains a steadfast companion in the world of auto repair, reassuring consumers that their prized possessions are in capable hands.
To ensure your vehicle maintains both its safety and aesthetic standards, consider the professional services offered by car detailing experts at https://schmicko.com.au. Their meticulous approach to car care extends beyond the surface, addressing both the structural and visual elements, creating a comprehensive solution for those who value safety, efficiency, and the allure of a well-maintained vehicle. Just as the automotive industry prioritizes safety and efficiency, these detailing services ensure your car is treated with the precision and care it deserves, keeping it in top-notch condition for the road ahead.
For enthusiasts seeking timeless automotive craftsmanship, navigating the realm of classic cars requires a blend of passion and expertise. Just as with modern vehicles, preserving the integrity of classic cars demands specialized knowledge and attention to detail. At classiccarsforsale.pro, we uphold the tradition of excellence, offering comprehensive services that include restoration, appraisal, and expert advice. Whether you’re a seasoned collector or a newcomer to the world of vintage automobiles, our commitment to quality craftsmanship ensures that every purchase through Classic Cars Deals is a testament to automotive history and a celebration of enduring style.
“Reduction in the fuel consumption through weight reduction to meet stringent emission regulations without compromising on safety is critical for the automotive industry. To meet these requirements, newer steels need to be developed which can overcome the strength-ductility trade-off and are commercially viable for widespread industrial production” explains Prof. Subramanya Sarma Vadlamani, a professor in the Department of Metallurgical and Materials Engineering at IIT Madras.
Prof. Sarma’s research is focused on trying to develop new steels that have high strength and ductility to be used as a material for making light-weight yet strong cars. The team has finally registered success in developing such a metal alloy and has also published their research work in a prestigious international journal Materials Science & Engineering A.
To develop such a material, the team used computational thermodynamics and kinetics or CALPHAD approach. Various important factors such as coatability, formability and weldability, that are required for automotive use of material were kept in mind while designing this material. Based on the computational results, scientists mixed manganese, carbon, aluminium, silicon, nickel and niobium elements in steel in a particular ratio. This new steel was then subjected to melting and thermomechanical processing to produce ultra-fine grains.
“The basic issue here was to produce the maximum amount of retained austenite fraction with very good chemical and mechanical stability and to impart it with an ability to transform slowly to martensite and to undergo massive twinning during deformation, thereby providing a rather continuous strain-hardening effect to prevent early failure. The other important issue here is how to realize the optimum stacking fault energy of the austenite fraction, which must lie within the overlapping range of stacking-fault energy for both transformation induced plasticity and twinning induced plasticity. The authors could achieve both by carefully controlling the chemical composition and the grain size and morphology of the retained austenite.” comments Prof. R. K. Ray, a former professor at IIT Kanpur, a world renowned materials scientist with expertise in steel technology.
Prof. VS Sarma Prof. K C Hari Kumar Prof. Sumantra Mandal Dr. CN Athreya Achintya Kumar Patra
Further, the team checked various properties of this newly developed steel by conducting experiments. They found that the steel had a yield strength of around 720 MPa – the amount of stress it can sustain before getting deformed or changing its shape. The steel had a tensile strength of around 1350 MPa which means that it can withstand 1350 MPa of stress of before fracturing. The steel was found to stretch or elongate around 26% at the maximum stress. These attributes, in combination, makes the developed steel much superior to the similar grades of steel that have been reported earlier.
These steels are coated with Zinc (referred to as Galvanising) to provide resistance to corrosion in service. Also forming and welding is widely used in fabrication of automotive structures. “Next, we aim to check the coatability, formability and weldability aspects of the developed material experimentally and carry out higher deformation rate studies to evaluate the crash resistance of this material,” adds Prof. Sarma.
The team is also planning to engage with steel and auto industries for the commercial use of their research results.
“Overall, this is a very commendable work that not only advances the boundary of science but at the same time gives more than a glimpse of a novel engineering material of the future,” adds Prof. Ray.
The team led by Prof. Sarma included his colleague Prof. K.C. Hari Kumar, collaborator Prof. Sumantra Mandal from IIT Kharagpur and PhD student Achintya Kumar Patra and postdoctoral fellow, Dr. C.N. Athreya.
Article by Aditi Jain
Here is the original link to the paper:
https://www.sciencedirect.com/science/article/abs/pii/S0921509321000253