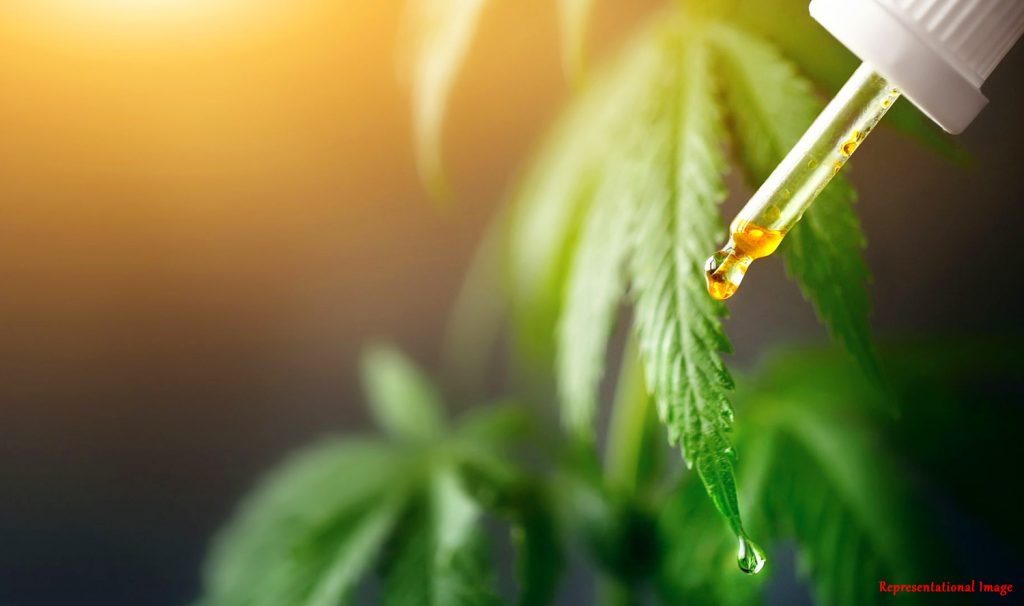
You may think the flow of a droplet on a solid surface is nothing to think about. But this simple phenomenon finds use in many forms of science such as physics, chemistry, material science and engineering.
This phenomenon finds use in the field of microfluidics. Microfluidics is the study of the manipulation of tiny amounts of fluids, in the range of microns (a millionth) or smaller sizes. Microfluidics find use in the fields of enzyme analysis, DNA analysis, proteomics, clinical pathology, etc. It is also an important phenomenon in proper drug delivery.
There are many ways to manipulate a droplet such as through the use of electrical, chemical, and magnetic forces to generate the motion of the droplet. However, these techniques need the droplet or surface to have special properties or require sophisticated equipment for the droplet to be manipulated and to flow.
The use of thermocapillary forces to manipulate the droplet and cause motion is interesting. Here the temperature is varied to cause flow of the droplet on the solid surface.
Various factors affect thermocapillary flow. These include – effect of volume of the droplet, contact angel hysteresis (activation energy required for movement of a droplet from one state to another on a surface), temperature gradient, droplet liquid etc.
It is observed that contact angle hysteresis is the major detrimental factor for thermocapillary migration. For this reason, studies usually focus on augmenting the thermocapillary forces or studying the motion of a droplet on a surface engineered to have low contact angle hysteresis.
It has been observed that the migration characteristics of a paraffin oil droplet are enhanced on a surface with grooves parallel to the direction of the temperature gradient compared to a surface without grooves.
In this study, the authors which include Mr. Srinivasa Sagar Kalichetty, Prof. T. Sundararajan, and Prof. Arvind Pattamatta from the Department of Mechanical Engineering, Indian Institute of Technology Madras, Chennai, India, have performed a numerical investigation to understand the limits in enhancing the thermocapillary migration velocity of a droplet due to lateral spread confinement on an oleophilic (having affinity towards oil) track.
Various studies were performed to understand the dynamics of flow. Three-dimensional simulations showed that reducing the width of the oleophilic track improves the droplet migration velocity only up to a specific track width. Further decrease in track width is seen to depreciate the enhancement in migration velocity. The spread length on the oleophilic track was found to have a similar variation with the track width.
These two trends are related because of the temperature difference in the droplet, and they determine the driving force governing the migration velocity characteristics.
A parametric study was also performed to assess the migration behaviour on oleophilic tracks with change in substrate temperature gradient, droplet volume, and contact angles within and outside the track.
This work will help in designing the microfluidic systems that employ thermocapillary migration or surfaces for tribologic (two surfaces in contact) applications.
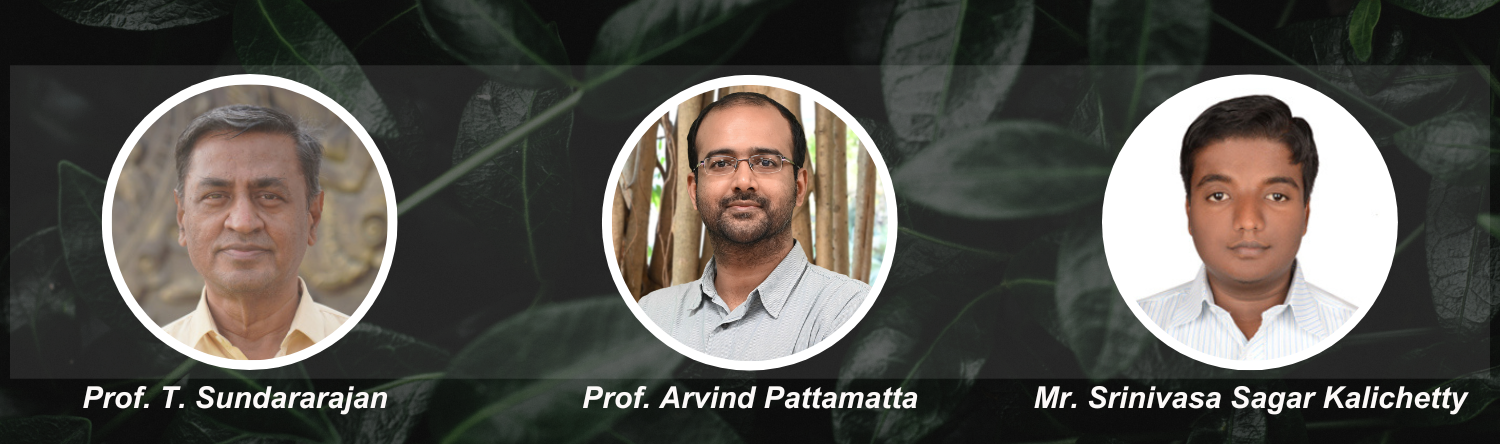
Prof. Cameron Tropea, Head of the Institute of Fluid Mechanics and Aerodynamics, Technische Universitat Darmstadt, Germany, gave the following detailed analysis of the work done by the authors: “The subject of capillary and microfluidic flows, although not perceived as commonplace or part of our everyday lives, is a field of tremendous importance, not only in the fields of engineering, but perhaps even more so in natural phenomena. For the layman, such flows are most easily illustrated in how a water drop would run off a plant leaf or down a window pane. The question of wettability and how liquids move across surfaces or in small confined channels is a science lying somewhere in the intersection of chemistry, physics, material science and engineering. It is therefore little wonder that this topic is often passed over in standard education curricula.
However, several groups at IIT Madras have devoted their research to such phenomena and Prof. Arvind Pattamatta in Mechanical Engineering, together with his co-authors Srinivasa Sagar Kalichetty and T. Sundararajan have addressed a very special topic in this domain, namely the movement of drops on surfaces due to thermocapillary forces. This arises when a temperature gradient exists over the expanse of the drop, usually induced by a non-uniformly heated surface. Under such conditions, the surface tension varies over the length of the drop and this induces motion of the drop on the surface. The work of Pattamatta attempts to predict such movement through numerical simulations, their approach having previously been validated using experimentally obtained data from literature.
The challenge of such numerical simulations is to properly capture the physics at the three-phase contact line, i.e. at the intersection of solid surface, liquid drop and ambient gas. This is not a trivial task, especially when the wettability of the surface is not uniform, but patterned. The wettability is expressed as a contact angle; however, this angle is neither constant when movement is involved, nor is it unique for a given drop volume on the surface. Using state of the art numerical schemes and model equations for this question of contact angle and contact line movement, the group of Pattamatta have computed a series of scenarios in which the thermocapillary movement of a drop on a wettable stripe patterned onto an otherwise non-wettable surface is predicted. The wettable stripe is known as oleophilic as opposed to hydrophilic simply because the drop is not water, but squalene. The prediction and systematic study of influencing parameters convincingly delineates limiting values of various quantities and reveals conditions under which maximum migration of the drop can be expected. This represents an important step forward in design and performance prediction of microfluidic devices.”
Article by Akshay Anantharaman
Click here for the original link to the paper