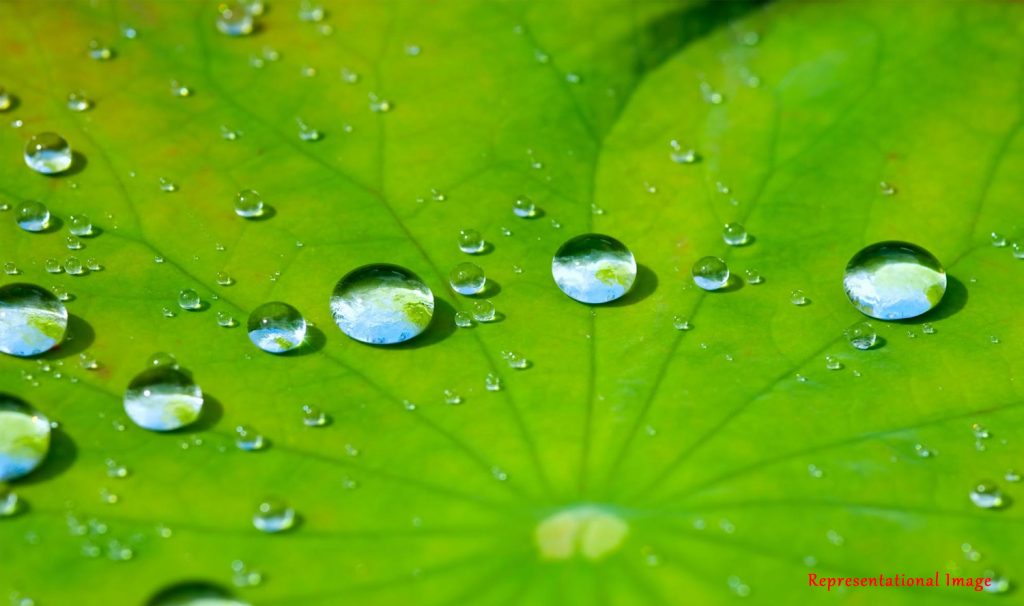
Understanding the flow at the point of contact of a liquid and a solid interface has many practical applications in industrial processes such as coatings, oil recovery, ink-jet printing, and chemical etching of surfaces. This intersection between a liquid interface and a solid is known as a contact line, and it separates the dry region of the solid from the wet.
A contact line can be static or dynamic and the corresponding angle that the liquid makes with the solid, within the liquid phase, is known as the static and the dynamic contact angle respectively; the dynamic contact angle being different from its stationary counterpart. Dynamic contact angles can be advancing or receding based on whether the contact line wets or de-wets the solid surface. Dynamic contact angles usually depend on the ratio of viscous to surface tension forces, called the capillary number.
At low speeds, a moving contact line remains straight. In such cases, the flow near the contact line during the wetting or de-wetting process is two-dimensional. Then, the liquid and solid interfaces would effectively form a wedge, with the contact line at the corner. In dynamic contact lines, the liquid at the liquid-gas interface moves, while the liquid at the solid-liquid interface is stationary. Then, the liquid on the contact line, which becomes part of both the interfaces, will have to move as well as remain stationary; an impossibility which results in a stress singularity and the usual equations of fluid mechanics to break down at the contact line.
A commonly suggested method to overcome the stress singularity is to introduce a region of slip on the solid surface in close proximity of the contact line. However, the flow fields in such slip models make the contact line behave as an obstacle to the flow. The experiments suggest otherwise, where a rolling motion is observed with the fluid being accelerated near the contact line.
When Reynolds number, which shows the amount of inertia with respect to the viscous forces, is large, viscosity dominated theory based on Stokes flow alone is not sufficient to describe the flow. Thus, in the case of fast moving liquids, which occur when the surface is non-wetting to the liquid, like water on lotus leaves, inertia is expected to influence the flow dynamics significantly.
For the first time (to the authors’ knowledge), the authors of this paper, which include Dr. Akhil Varma, the main and primary author of this paper, Prof. Anubhab Roy, and Prof. Baburaj A. Puthenveettil, from the Department of Applied Mechanics, IIT Madras, obtain singularity free inertial corrections to explain the behaviour of the flow near fast moving contact lines.
Dr. Akhil Varma Prof. Anubhab Roy Prof. Baburaj A. Puthenveettil
Till now, only the Stokes flow was taken into account for the behaviour of a moving liquid near a contact line, which however could not explain the behaviour of fast-moving liquids at the solid interface. When inertia is taken into account, they show that the flow accelerates as it approaches an advancing contact line. For a receding contact line, the flow accelerates as it leaves the contact line; these are in agreement with experimental observations. They obtain expressions for the free surface velocities for fast moving contact lines from which they show that the free surface velocity for fast moving contact lines depend on the distance from the contact line, unlike in the case of slow moving contact lines. Surprisingly, a perfectly wetting and a perfectly non-wetting surface is shown to have no effect of fast motion of the contact line on the flow field. More importantly, they show that even though the flow fields are significantly affected by the fast motion of the contact lines, the contact angles are not at all affected. This new finding shows that the many existing contact angle models for fast motion of contact lines to be superfluous.
Prof. Harish N. Dixit, from the Department of Mechanical & Aerospace Engineering, IIT Hyderabad, gave the following critical comments on the study: “The motion of a moving contact line is perhaps one of the most challenging problems in fluid mechanics owing to the existence of a non-integrable singularity at the contact line. This singularity appears due to our limited understanding of the dissipation mechanism near a moving contact line. In an earlier study, Puthenveettil et al. (2013) had studied motion of drops on inclined surfaces at high speed, or, to be more precise, in the high inertia limit. In the current study, Prof. Puthenveettil’s group examines how the flow field in the vicinity of a moving contact line is altered due to inertia. The template followed by the authors is standard, i.e., to understand the flow in a wedge between a moving plate and a fluid interface. Since there is no natural length scale in such a set-up, the radial location from the contact line, a proxy to the well-known Reynolds number, is used by the authors to carefully carry out a regular perturbation expansion. The study reveals that inertia causes significant alteration to the flow field from classical solutions present in the literature. For example, in the inertial solution, the velocity along the interface depends on radial location from the contact line unlike the Stokes flow solution. The authors also provide a detailed recipe for removing the singularity in the streamfunction, a feature observed in many other self-similar flows, though the exact recipe depends on the nature of the problem. In summary, the work of Puthenveettil et al. further adds to the rich physics of moving contact lines and will surely spur more experimental theoretical efforts in this field. In my own research group, we are keenly studying the results presented in this paper.”
Article by Akshay Anantharaman
Here is the original link to the paper:
https://www.cambridge.org/core/journals/journal-of-fluid-mechanics/article/abs/inertial-effects-on-the-flow-near-a-moving-contact-line/4E7417A8330C7012452D2ED649726AA0