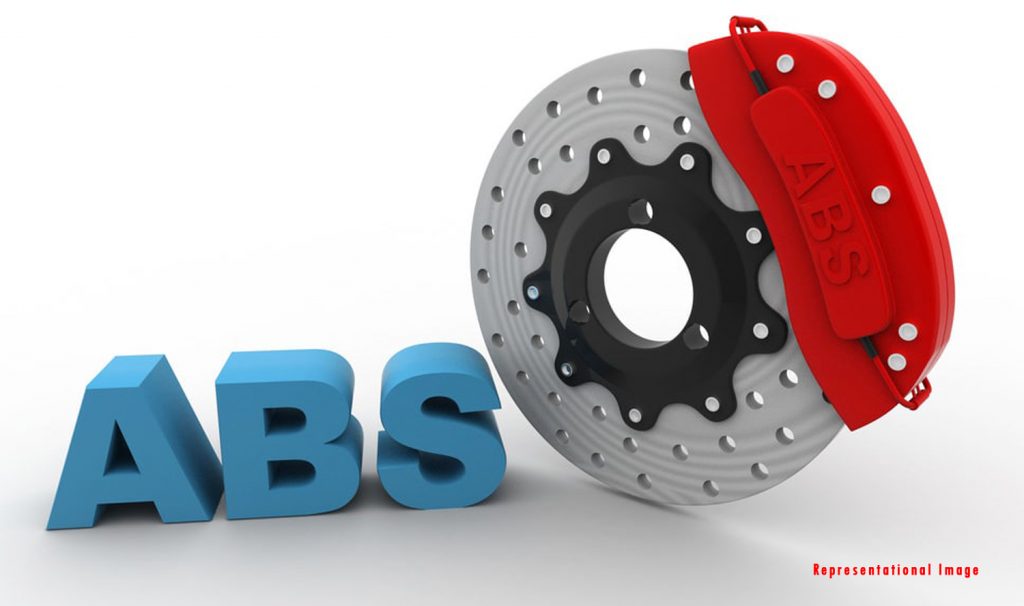
In India, heavy commercial road vehicles (includes buses, trucks etc.) contributed 28.8% of total road accidents and 32.6% of total fatalities in the year 2018. The World Health Organization places road accidents as the eighth most common cause of death, which is expected to become the seventh most common cause of death by the year 2030.
Road accidents and associated fatalities can be reduced by improving vehicle dynamic stability, and this can be achieved through various active safety systems such as Antilock Brake System (ABS), yaw stability systems, traction control systems, and roll stability systems. Maintaining vehicle stability during braking becomes particularly important since wheel lock (a wheel is said to be locked when it stops rotating while the vehicle is still in motion) would result in loss of stability and potential accidents. Motivated by this, the Government of India has mandated ABS in Heavy Commercial Road Vehicles (HCRVs). In fact, the National Highway Traffic Safety Administration, USA, reported that the accidents associated with HCRVs reduced by 13% with ABS.
Most of the conventional HCRVs (those using an internal combustion engine) use a pneumatic friction brake system. The main challenges of using a pneumatic friction brake system are its significant time delay and lower bandwidth. In electric vehicles (EVs) and hybrid electric vehicles (HEVs), a regenerative brake system is used. This brake system has a higher bandwidth compared to a pneumatic friction brake system.
With regenerative braking, a part of the vehicle’s kinetic energy is converted to electrical energy and stored in the battery for future use to drive the vehicle. This helps to reduce the fuel consumption thereby reducing vehicle tailpipe emissions in EVs and HEVs compared to a conventional vehicle. However, regenerative braking alone cannot deliver adequate deceleration. Hence, it cannot replace the pneumatic friction brake. Thus, in EVs and HEVs, the total brake force is distributed between friction braking and regenerative braking, which is called co-operative braking.
The motivation of this work is explained by considering the challenges associated with electrified HCRVs. During braking, the dynamic load transfer from the rear to the front wheels in HCRVs is more significant than in passenger cars. Further, the brake system is designed and developed by considering a fully loaded condition, and this can result in potential stability issues while braking an unladen vehicle.
Considering the non-linearity in the longitudinal force developed by a tire and the parametric uncertainties (road surfaces, static and dynamic load variation), a robust nonlinear controller is recommended for Wheel Slip Regulation (WSR). Among the robust nonlinear controllers, sliding mode controller (SMC) is widely used. Hence, this research developed an SMC based active co-operative braking strategy for regulating the regenerative braking torque during WSR application for electrified HCRVs. The scope of this work is illustrated in Figure 1.
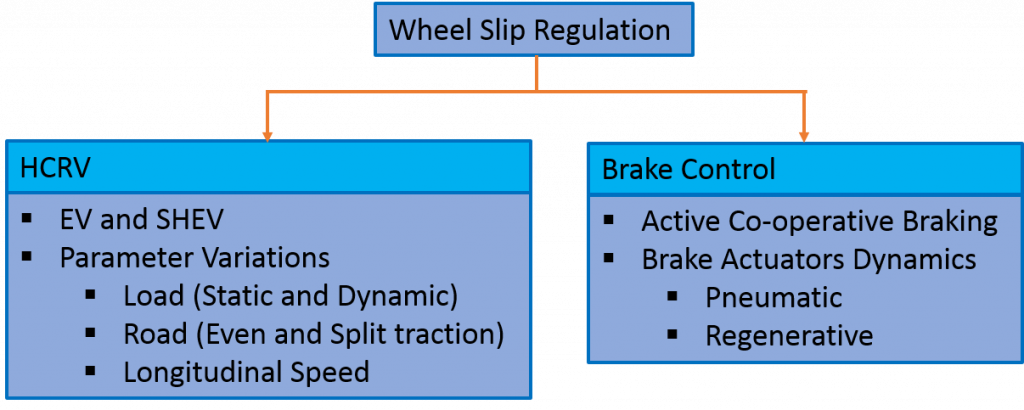
During the braking of a rear-wheel driven electrified vehicle, both regenerative and friction braking are available on the rear (driven) wheels, while only friction braking is available on the front wheels. In the proposed active co-operative braking strategy, friction braking is used to maintain the wheel slip ratio corresponding to the maximum braking force, and regenerative braking is used to reject the disturbances and handle the uncertainties. To minimize the slip tracking error, the proposed co-operative strategy maintains the actual wheel slip ratio near-by the desired slip ratio (Figure 2).
The reasons for regulating regenerative braking to minimize the tracking error are as follows:
1. The amount of regenerative braking torque provided by the motor is less than the total braking torque for a full pedal application on a dry road. Hence, friction braking cannot be replaced by only regenerative braking.
2. The time delay and time constant of the regenerative brake system are lower than those of the pneumatic friction brake system. Therefore, it possesses higher band width and improves braking performance.
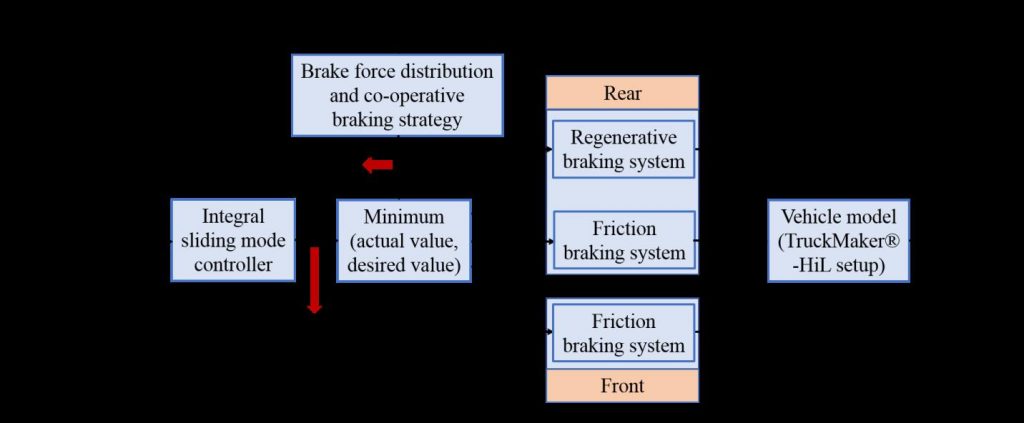
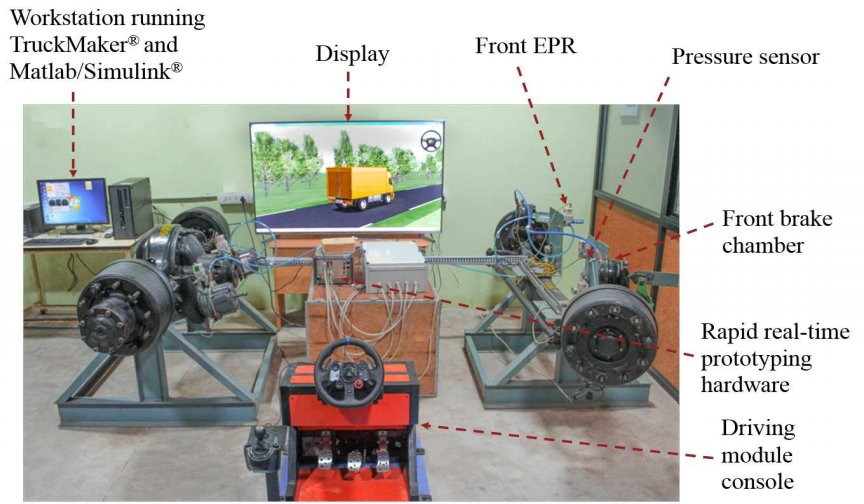
The proposed co-operative braking strategy was evaluated in a Hardware-in-Loop experimental setup (Figure 3) equipped with the IPG TruckMaker® vehicle simulation software and tested for various operating conditions. Since electrified powertrain hardware components were not included in the experimental setup, regenerative braking was simulated through an appropriate mathematical model.
The main contributions of this study are as follows:
1. The impact of reaching law and the sensitivity of its parameters on WSR have been investigated.
2. The robustness of the controller was tested by considering the variations in initial braking speed, payload, and road surfaces.
3. The advantage of regenerative braking was studied for wheel slip ratio tracking during the braking of electrified HCRVs.
Mr. Kesavan Valis Subramaniyam Prof. Shankar C. Subramanian
Dr. Frank Kienhofer, of the University of the Witwatersrand, Johannesburg, South Africa gave his opinion on this research as follows: “The authors Kesavan Valis Subramaniyam and Professor Shankar C. Subramanian have detailed a very clever method to improve the braking of trucks or heavy commercial road vehicles in their paper “Electrified Vehicle Wheel Slip Control Using Responsiveness of Regenerative Braking”. The novel idea is to use the conventional pneumatic braking system for the heavy lifting and the regenerative braking system for the controlled finesse to keep the braking amount at the optimal amount; much like a ballet duet. The best architecture to integrate the pneumatic and regenerative braking systems is detailed in the paper. The proposed control strategy is evaluated on a so-called hardware-in-the-loop rig in which actual braking hardware is used to brake a simulated vehicle. In this way the testing embraces both physical testing with no simulation accuracies for the braking system which is the focus, and simulation of a vehicle which is cheaper, more repeatable, and safer. The results of the research are excellent with a reduction in stopping distance of 2–4%. This may seem a trivial improvement but consider a truck typically takes 150 m to stop if travelling at 100 km/h; and the improvement is 3–6 m. That is more than a car length and the proposed algorithm could conceivably make a significant improvement to truck safety if implemented.”
Article by Akshay Anantharaman
Here is the original link to the scientific paper:
https://ieeexplore.ieee.org/document/9056843