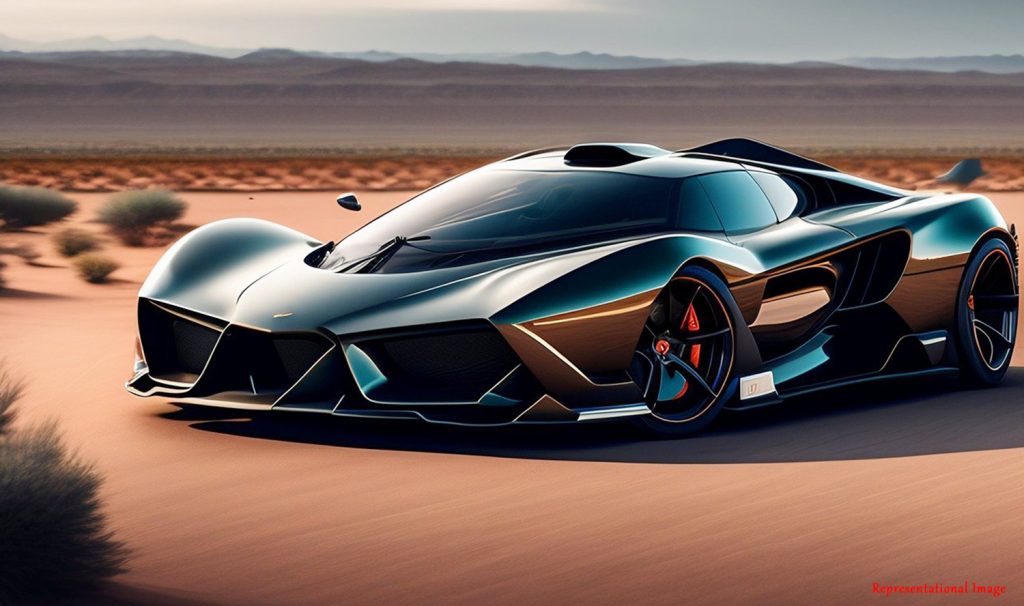
Have you ever wondered how the sleek and smooth surfaces of airplanes, automobiles, and several biomedical devices are modelled? These are carefully designed with free-form surfaces and these products are made with utmost care and accuracy. Parametric formulations like Bezier, B-spline, and NURBS (Non-uniform Rational B-spline) are used for modeling the free-form surfaces and profiles.
Designing these surfaces is no easy task, as every measurement needs to be perfect. Thus many tools such as coordinate measuring machines (CMM) and non-contact scanners are used to inspect the accuracy of these surfaces.
The output from these devices, called the measured point-set, needs to be aligned with the reference profile (or surface) and later inspected for the profile error. This process of alignment is called registration.
Registration is accomplished in two phases, namely coarse registration and fine registration. During the coarse registration stage, the measured point-set is initially aligned with the reference profile. In the fine registration stage, the coarsely registered measured point-set is brought closer to the reference profile, ensuring that each of the surface’s profile errors is less than δ/2. δ (delta), represents the distance between two offset profiles as specified by the Bureau of Indian Standards (BIS), and it denotes the designer-specified maximum allowable profile error.
Usually, a method known as the point-inversion method is used to verify this accuracy. It has relatively high time complexity. Although point-inversion method is one of the most accurate methods to check the accuracy of the surface, it has drawbacks. This method is iterative (repetitive), and there always exists a trade-off between the point density and the accuracy of profile error estimation. Therefore, there is a need for a discretization strategy and profile error estimation technique from the discretized profile.
In this study conducted by Mr. Hari Ganesh S and Prof. G. L. Samuel from the Department of Mechanical Engineering, Indian Institute of Technology (IIT) Madras, Chennai, India, a two-stage framework based on the concept of the Voronoi diagram was proposed for the profile error estimation of 2D free-form profiles. A Voronoi diagram is a partition of a plane into regions that are close to each of a given set of objects.
In this method, the first stage involves preparing a discretized profile for the measurement process. In the second stage, the profile errors are estimated from the measured point-set using the discretized profile.
The results were compared with simulated NURBS (Non-uniform Rational B-spline) profiles as well as practically measured CT-scanner data of two machined airfoils modelled as NURBS profiles.
The results show that the accuracy of the proposed frameworks is on par with that of the point-inversion method, and is at least 56 percent faster than the generally used point-inversion method. This shows that the proposed method can serve as a rapid and precise alternative for coordinate measuring machines (CMM) (operated in continuous scanning mode), computer numerical control (CNC) machine-based (in-situ), and vision-based 2D profile inspection.
Future scope can be to extend this method to 3D surfaces, partial scans of measured data, and free-form objects represented as point-clouds and unstructured meshes. The accuracy of profile error estimation can be enhanced through the utilization of new interpolation techniques that use the structure of the Voronoi diagram.
Prof. Sanjay S. Pande from the Mechanical Engineering Department of the Indian Institute of Technology (IIT) Bombay, Mumbai, India, gave his analysis of the work done by the authors with the following comments: “This paper presents an interesting approach on the use of Voronoi diagram for the inspection of 2D free form surface profiles represented as point sets. Both coarse and fine registration (inspection) algorithms are proposed, implemented and verified using the simulated (NURBs) and real (manufactured) 2 D profiles. The proposed approach is accurate and fast (~56%) compared to the reported techniques. It would be interesting to see the extended application of the Voronoi diagram technique for the inspection of 3D free form profiles.”
Article by Akshay Anantharaman
Click here for the original link to the paper