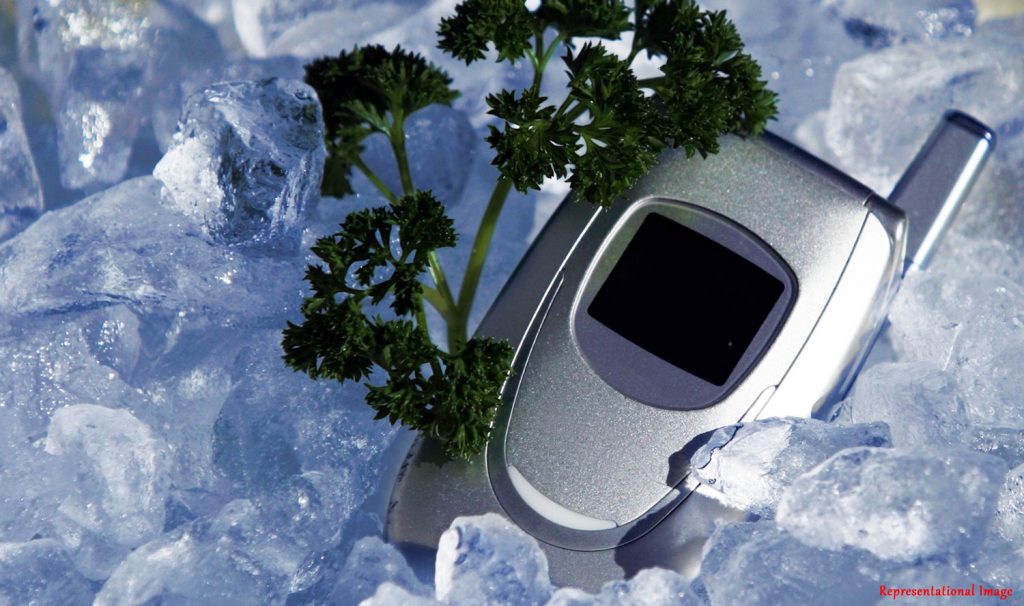
As technology advances, the size of devices is shrinking, along with high power output. Along with these advances, comes the need for these devices to have efficient and effective heat transfer.
In order to do this, researchers have come up with many methods for effective heat transfer such as two-phase cooling, jet impingement cooling, spray cooling, and mini/microchannel heat transfer. Of these, mini/microchannel heat transfer has attracted a lot of attention.
Mini/microchannel heat transfer has many advantages such as superior heat transfer performance, compact size, smaller volume per heat load, low operational cost, etc.
The problem with mini/microchannels is that the heat transfer capability is limited by the laminar flow observed in small dimensions. Laminar flow happens when the fluid travels in smooth or regular paths. This causes boundary layer formation that restricts fluid mixing and heat transfer.
In order to overcome this limitation, researchers have come up with different active and passive heat transfer enhancement techniques such as pin fin arrays, vortex generation, flow disruptions, acoustic vibrations, magnetic field, electric field, etc. Of these, vortex generation was considered by the authors of this paper.
Vortex generation along with the use of geometrical obstructions such as fins and flexible flaps in mini/microchannels is a passive method to improve the heat transfer rates. But these flow protrusions lead to additional geometric drag causing a notable increase in the pumping power requirements. In order to overcome this limitation, active vortex generation using electric field has been considered.
Electrohydrodynamic (EHD) flow based heat transfer has several advantages such as simple design, easy control, quick-response, low power consumption, no noise and vibration etc.
Usually, charge injection based ion-drag pumping of dielectric fluids is considered along with EHD based vortex generation. However, this leads to deterioration of electrodes and dielectric fluid.
Thus EHD conduction pumping was considered, which is based on charge generation by electric field enhanced dissociation of ions. The free charges undergo dissociation and recombination in the presence of an external electric field.
In general, the rate of dissociation and recombination are equal. However, there is a threshold voltage where the rate of dissociation exceeds the rate of recombination. This phenomenon is known as the “field-enhanced dissociation”, or the “Onsager-Wien effect”.
Because of Onsager-Wien effect, a layer of free charges known as “hetero-charge layer” is formed over the electrodes. The residual charges move towards the oppositely charged adjacent electrodes, while inducing a fluid motion.
Ideally, the net fluid flow caused by the movement of opposite charges is zero. But electrodes with different surface areas can be used to generate a net fluid motion.
The Onsager-Wien effect has the advantage that it requires lower threshold voltage and the net flow rate and velocities generated by this effect is smaller than that generated by ion-drag pumping. This makes it suitable for mini/microfluidic applications.
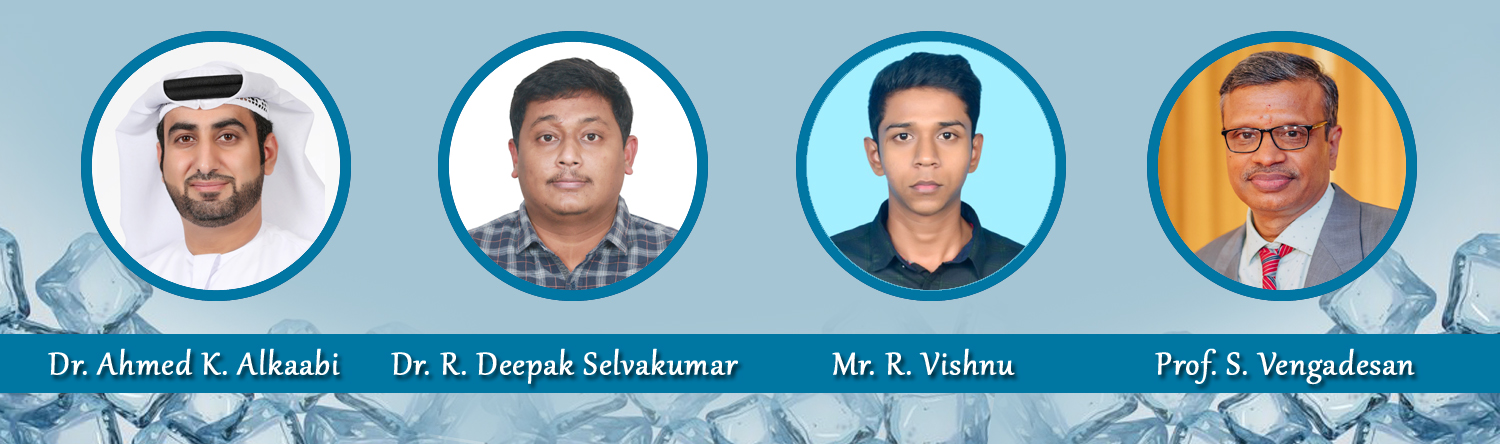
In this study, conducted by Mr. R. Vishnu and Prof. S. Vengadesan from the Department of Applied Mechanics, Indian Institute of Technology Madras, Chennai, India, and Dr. R. Deepak Selvakumar and Dr. Ahmed K. Alkaabi from the Department of Nuclear Engineering and Emirates Nuclear Technology Center (ENTC), Khalifa University of Science and Technology, Abu Dhabi, United Arab Emirates, for the first time, to the best of the authors’ knowledge, a new design of a mini/microchannel has been proposed that uses EHD conduction pumping as an active heat transfer enhancement technique.
A numerical analysis of active vortex generation by Onsager-Wien effect based EHD conduction pumping in a three-dimensional minichannel was performed.
The results of this study indicate that active vortices generated by Onsager-Wien effect using thin plate electrodes can effectively deplete the boundary layer and increase the heat transfer in a laminar, single-phase minichannel flow economically.
A maximum of 48.25 percent increase in heat transfer was achieved. For all the cases considered in this study, the achieved heat transfer was found to be higher than the increase in pumping power requirement.
Prof. Danesh Tafti, William S. Cross Professor and ASME Fellow, from the Department of Mechanical Engineering, Virginia Tech, USA, acknowledged the importance of the work done by the authors with the following comments: “This study tackles the important problem of electronic cooling by studying a novel pathway for enhancing heat removal using electrohydrodynamics (EHD). Unlike other methods utilizing EHD that requires the application of large voltages to have meaningful increases in heat transfer, the current method builds on past work on the Onsager-Wien effect that requires much smaller electric field strengths to produce flow instabilities that lead to heat transfer enhancement. By clever placement and sizing of electrodes, the study shows that the amount of heat that can be removed from the silicon chip can be enhanced by 50% under certain conditions while using only 20 mW of additional power and without a substantial increase in the power required to pump the fluid through the channel. This is a significant result which has potential for further development by combining it with other passive means of heat transfer augmentation.”
This work was further validated by Prof. Gaurav Tomar, from the Department of Mechanical Engineering, Indian Institute of Science, Bengaluru, India with the following comments: “In the article “Active vortex generation and enhanced heat transfer in a 3D minichannel by Onsager-Wien effect” by Vishnu et al., authors have shown that electric field induced flow can be employed to enhance the heat transfer by around 50% at a very small additional cost of electric power consumption. This is a multiphysics problem with coupling between fluid flow, heat transfer, electric field and flow of charges. Authors perform high fidelity calculations and capture the generation of small vortices in the vicinity of an electrode due to the Onsager-Wien effect. The small scale vortices lead to local mixing in the fluid thus enhancing the overall heat transfer coefficient. The results are particularly of interest in the design of micro and mini channel heat sinks that can be readily employed in electronic devices such as smart phones, sensors and potentially in electronic cooling in satellites.”
Article by Akshay Anantharaman
Click here for the original link to the paper