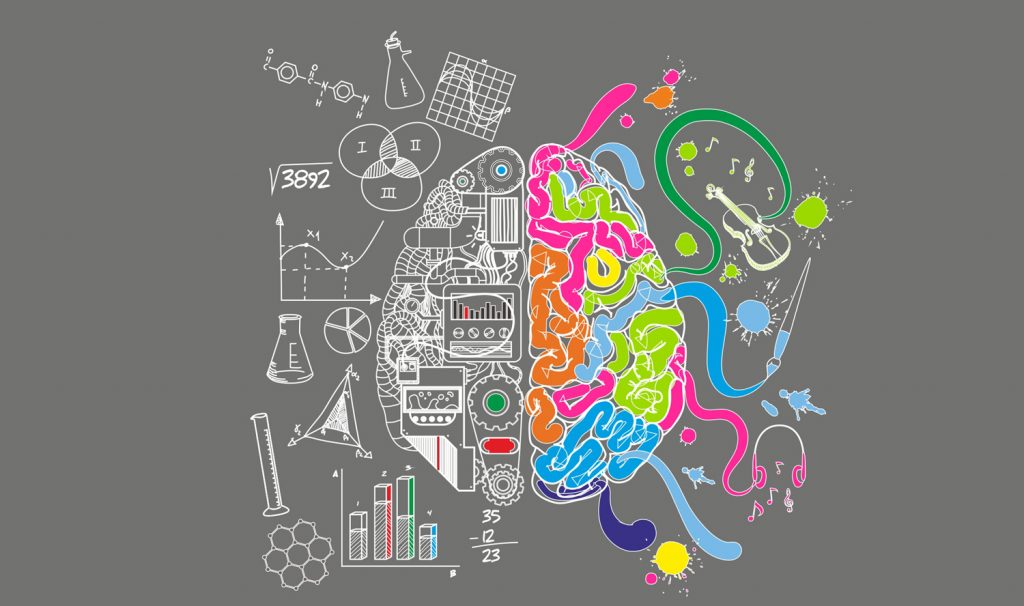
They say music feeds the souls. And musical instruments such as guitar, piano, trumpet and violin etc. when team up in an orchestra, produce a melody that not only stimulates our minds but also leave a lasting impression by touching our hearts. The harmonious sound waves that reach our ears are caused by the vibrations that emerge from these instruments. However the vibrations which are euphony for music lovers are a cacophony for the automobile industry as they damage machines.
Unlike musicians, the automobile engineers dislike vibrations because they create imbalance in vehicles, cause wear and tear and also give discomfort to the riders. Vibrations in a vehicle are mostly created due to the ill-designed engine. To make a ride smoother, the engineers work to minimize the vibrations by a process called vibration damping. In this process, the vibration energy is either absorbed or changed to reduce the amount of energy which gets transmitted to the main body or structure. Depending on how this process is carried out, the damping is categorized as active damping or passive damping. In active damping, a sensor measures the force of the vibrating unit and generates a force to decrease the unwanted motion. In passive damping, however, mechanical components such as shock absorbers, spring blades along with their inherent material properties are employed to dampen the vibrations. Passive damping is a preferred approach in the automobile industry as it is less complex and inexpensive.
Prof. Prathap Haridoss and his research team at the IIT Madras have been experimenting with materials which can mitigate the effect of vibrations on vehicle performance. In their latest research which is published in the journal Nanoscale Advances, the team shows the efficacy of various structures and forms of carbon nanotubes in damping vibrations when incorporated in the polymer.
Carbon nanotubes (CNT) are tiny cylindrical molecules which are rolled up sheets of single layer carbon atoms. Belonging to the class of nanomaterials, carbon nanotubes have exceptional properties that have been used in many applications where the aim is to enhance mechanical, electrical or thermal properties. The team decided to test the applicability of two forms of carbon nanotubes: straight and coiled, in damping the vibrations when incorporated into epoxy resin-a type of plastic.
“Polymer and its composites are reported to have higher damping characteristics. Interfaces in these composites contribute the damping. The addition of nanoscale particles increases the amount of interface due to their high specific surface area. Interfacial stick-slip, CNT-CNT sliding, and inner tube oscillation are the reported mechanism in polymer CNT composites. However, there are no reports on the effect of different structure and morphology of CNT on vibration damping characteristics of polymer/CNT composites. This study explores this aspect,” says Prof. Prathap Haridoss who is a professor at IIT Madras and the leader of the research team.
For the study, the researchers produced epoxy resins containing straight and coiled carbon nanotubes. Next, these composites were subjected to vibration tests to understand the effect of two types of carbon nanotubes on vibration damping. They observed that nanocomposites containing straight carbon nanotubes have higher vibration damping than those containing the coiled ones.
“The results of this study show the importance of the structure and morphology of reinforcing materials, here CNT, on the vibration damping characteristics of the bulk composite. We have already studied some of the other aspects of polymer/CNT composite to obtain enhanced damping characteristics. The results of this study can be implemented in the aerospace and automobile industry which use a lot of plastic components that have to be free from the vibrations of their engine,” adds Prof. Haridoss.
The scientists reasoned that straight nanotubes provide better damping effect as they have higher number of inner tubes and consequently they result in higher inner tube oscillation. However, kinks and bends in coiled nanotubes do not allow inner tube oscillations hampering their damping capacity.
“In this work, the structure and properties of the multiwalled carbon nanotubes are effectively utilized in epoxy matrix to dissipate energy that enhances vibration damping of the nanocomposite. Light weighting with vibration damping enhancement is a powerful combination that offers many possible technological applications in automotive, aerospace and marine sectors. The development of state-of-the-art light weight nanocomposite with better damping property, by exploring and unlocking the true potential of the arc discharge synthesized nanotubes paved a new way in research and technology,” commented Dr. Joseph Berkmans, Senior Manager at Advanced Materials Petrochemicals at the Reliance Industries limited, who is an expert in the same field but is not connected to this study.
Anand Joy
Dr. Susy Varughese
Dr. Anand K. Kanjarla
Dr. Sankaran S
Dr. Prathap Haridoss
The research was carried out by Anand Joy as part of the team studying this aspect, consisting of Professors Prathap Haridoss, Sankaran S, Susy Varughese, and Anand K. Kanjarla.
Link to the article: https://pubs.rsc.org/en/content/articlelanding/2020/na/c9na00812h#!divAbstract
Photo Caption: Anand Joy, Prof. Susy Varughese, Prof. Anand K. Kanjarla, Prof. Sankaran S. and
Prof. Prathap Haridoss