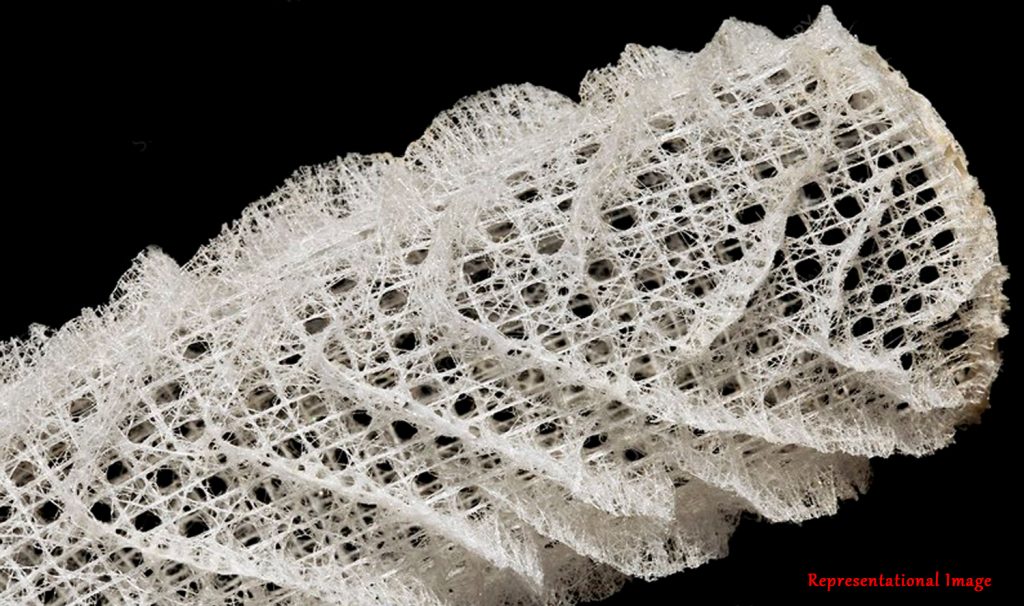
Lightweight materials are in high demand in a variety of industries from automotive to aerospace. To gain inspiration for such materials, we don’t have to look further than biological examples. For example, the triply periodic minimal surface (TPMS) gyroid was found in butterfly wing scales, and diamond surface in exoskeletons of beetles and weevils.
One of the ways to design lightweight structures is by using lattice structures. Lattice structures are a kind of lightweight porous materials that comprise periodical or random microstructural architecture. Lattice structures have potential applications in energy absorption, load carrying, heat dissipation, tissue engineering, battery electrodes, etc.
Mr. Deepak Sharma Dr. Somashekhar S. Hiremath
In this study conducted by Mr. Deepak Sharma and Dr. Somashekhar S. Hiremath from the Department of Mechanical Engineering, Indian Institute of Technology Madras, Chennai, India, a sea sponge called Euplectella aspergillum (E. aspergillum), commonly known as Venus’ Flower was used to derive bio-inspired lightweight structures. To the knowledge of the authors, this is the first time E. aspergillum has been used to obtain energy absorption in the fabricated lightweight structures.
The architecture of this sponge consists of square lattices with diagonally reinforced skeletal elements. This structure helps to increase the material resistance to global buckling. The image below shows the design approach for a unit cell of the lattice structure of E. aspergillum.
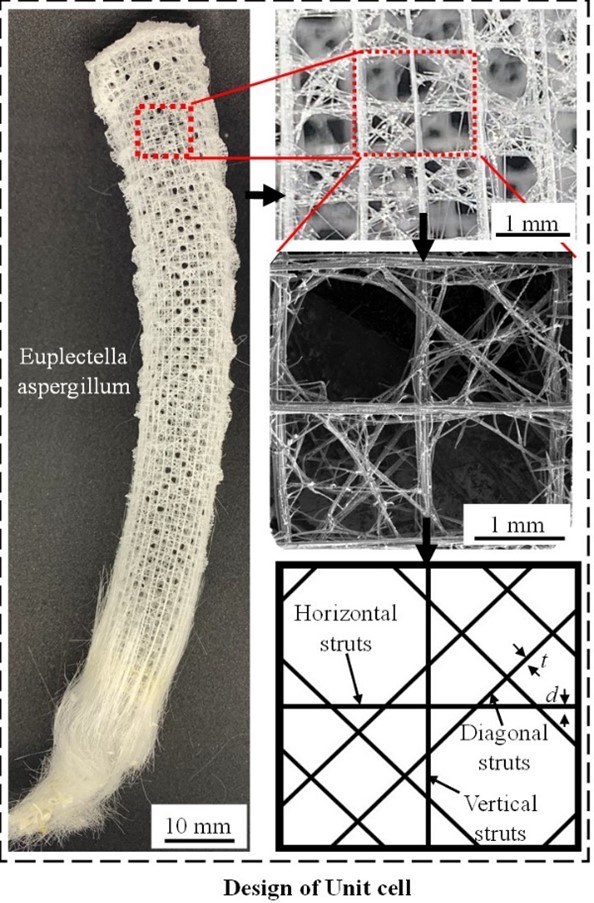
The deformation-induced local buckling behaviour of this lightweight E. aspergillum-based lattice design showed its suitability for energy absorption application. The long and flat plateau region of this sponge design helps the energy absorption to occur at a relatively constant stress value.
Structures are fabricated using the Fused Filament Fabrication (FFF) process with Thermoplastic Polyurethane (TPU) material. The FFF 3D printing machine and fabricated structure are given below:
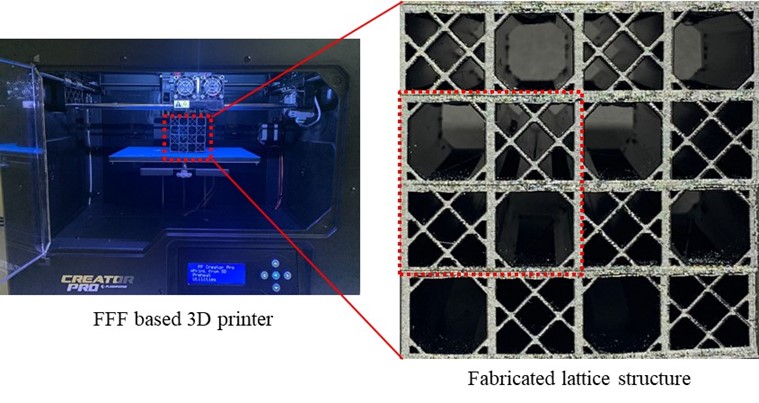
The energy absorption behaviour is studied under uni-axial static compressive loading conditions using numerical simulations and then the results are validated with experimentation.
The designed and fabricated structures showed good energy absorption properties with a long and stable plateau region. Local buckling resulted in stable energy absorption. The main objective of this experiment was to study the effects of design parameters of bio-inspired lattice structures on energy absorption performance.
To summarize, the current paper focused on bio-inspired Euplectella aspergillum based lattice structures for energy absorption applications. The stable energy absorption response can be used to develop better energy absorbers and suggests its potential for dampers, actuators, cushions, packaging materials, etc.
Dr. Mamilla Ravi Sankar, from the Department of Mechanical Engineering, Indian Institute of Technology Tirupati, Tirupati, India, gave the following comments on the authors’ work: “Lattice structures are one of the new concepts that can be mostly possible by Additive manufacturing (3D Printing). In the current study lattice structures are designed and fabricated by nature inspired structures. It is very nice that nature inspired lattice structures are used for energy absorption applications. The effect of the Lattice structure strut thickness, relative density, and unit cell size on the energy absorption is studied both experimentally and numerically.
The authors designed the structures to increase the energy absorption capacity with a stable plateau region without compromising the mean plateau stress. The bio-inspired lattice structures showed a local buckling other than the global buckling mode of deformation. The cyclic loading–unloading of the structures was also carried out to study their compressive behaviour and repeatability. The structures underwent a softening effect over the first cycle and became stable from the second cycle onwards. Hence, the improved energy absorption capacity, stable post-yielding stress, and high mean value stress can be used to develop better energy absorbers.”
Article by Akshay Anantharaman
Here is the original link to the paper:
https://www.sciencedirect.com/science/article/pii/S0263822321015208