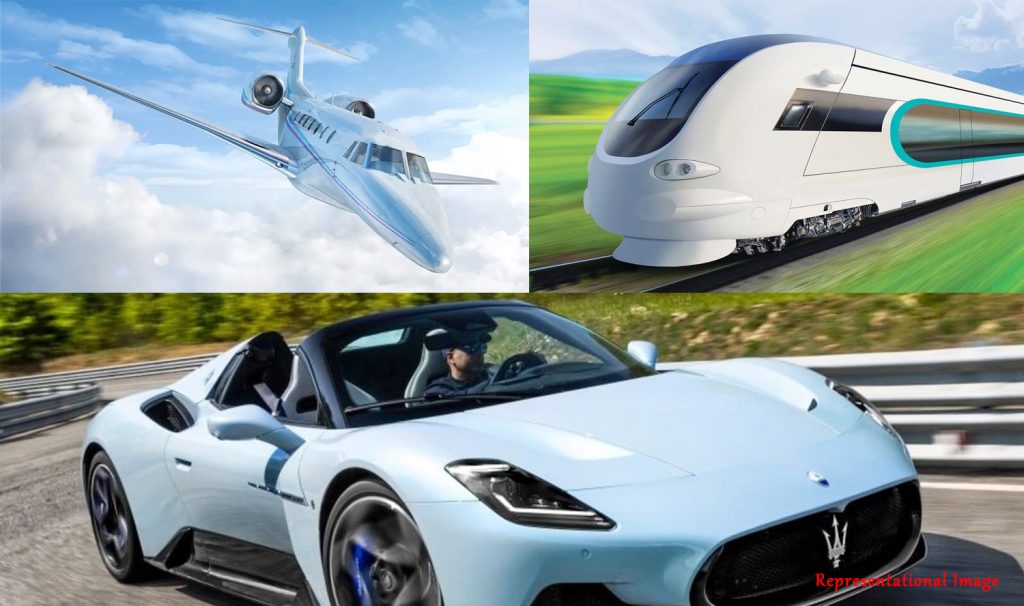
In the manufacturing industry, free-form surfaces and profiles have a wide range of applications in modelling versatile components which can be used in sectors such as the automobile, biomedical, and aerospace industries.
Due to the inherent limitations of the manufacturing processes, the shape of the free-form surfaces and two-dimensional profiles of the products manufactured will not be the same as that of the ideally desired surface.
In order to reduce errors in measurement, coordinate-measuring machine (CMM) is used to measure the geometry of physical objects by sensing discrete points on the surface of the object with a probe. This equipment and the associated software are used for accurately evaluating the profile deviations of free-form components.
Generally, the points measured by the CMM are either fitted or registered with the continuous reference profile. The profile deviation is estimated using the point-inversion technique with relatively high time complexity. Thus, there is a need for an alternate method for quick and accurate estimation of profile deviations.
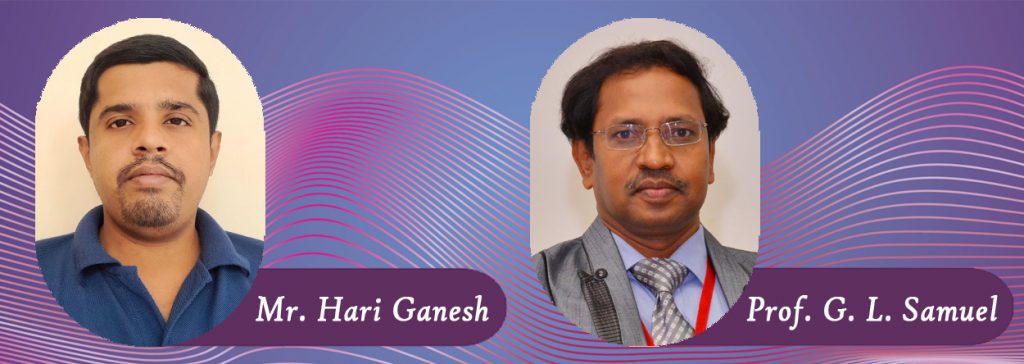
In this study conducted by Mr. Hari Ganesh and Prof. G. L. Samuel from the Department of Mechanical Engineering, Indian Institute of Technology (IIT) Madras, Chennai, India, a contact type CMM operated in discrete scanning mode was used for measurement of the free form components.
A two-stage methodology was developed for estimation of deviations in free-form profiles. This method is based on the concept of poles and pole radii extracted from the Voronoi diagram of the discretized profile. A Voronoi diagram is a partition of a plane into regions close to each of a given set of objects.
The two stages of the methodology are as follows:
1. Profile discretization and poles extraction.
2. Measurement and estimation of profile deviation
In the first stage, the global poles extract algorithm discretizes the profile adaptively around each sample point and simultaneously computes the Voronoi diagram and global poles data of the discretized profile.
In the second stage, the profile deviation estimate algorithm is used to calculate the absolute normal distance using the discretized point-set, its Voronoi diagram, and its corresponding global poles or local poles data.
The proposed method was found to be accurate, requiring lower execution time, thus making it suitable for CMM based inspection and in-situ inspection of free-form profiles in modern CNC (Computer Numerical Control) machines. The proposed work can be extended for inspection of three dimensional surface profiles measured using CMM operated in continuous mode.
Prof. Satish Bukkapatnam from Texas A&M University, who is also Director, TEES Institute for Manufacturing Systems, gave his views on the importance of the work done by the authors with the following comments: “This paper from Dr. Samuel group is a straightforward and elegant application of a rather well-known concept from computational geometry literature, known as the nearest-point Voronoi diagram, for capturing errors geometric profiles. Their algorithm for profile error estimation is quite simple, computationally efficient and appears to be easy to implement. In the current Industry 4.0 era, the estimation algorithms used in manufacturing contexts should not just meet the desired accuracies, but also be computationally efficient and fast, and should not consume excessive resources such as memory and storage. I think the present method satisfies these criteria. More importantly, the computer codes of these classes of algorithms are the right candidates to be on cloud platforms. These codes could serve as part of the toolbox of a designer, or a quality engineer, and several R&D professionals.”
Article by Akshay Anantharaman
Click here for the original link to the paper