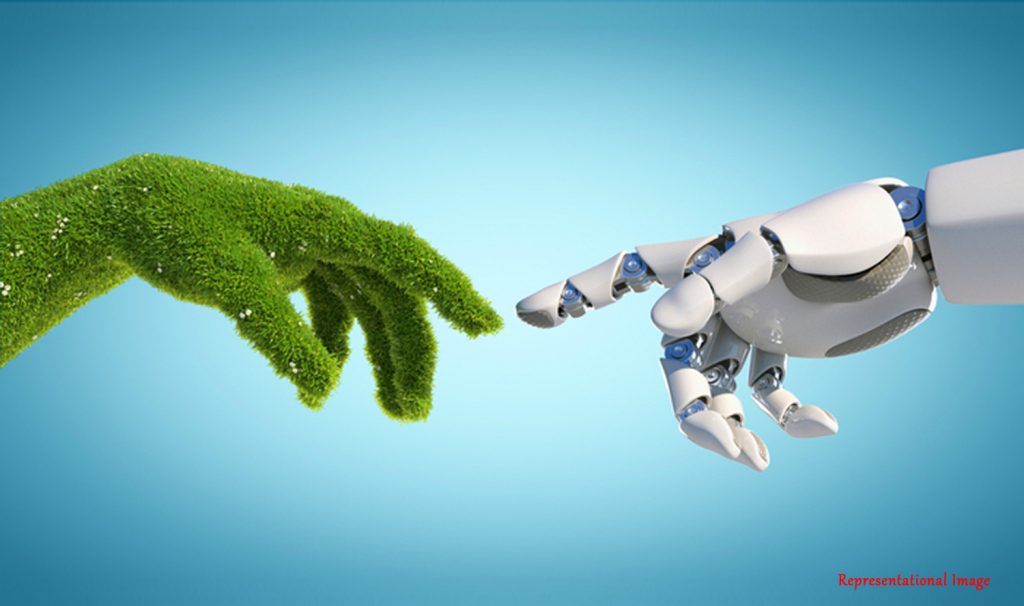
Nature inspired designs led to significant breakthroughs in science and technology. For example, consider the case of bumpy nodes known as tubercles on the fins of humpback whales. These bumpy nodes help the whale to cut through water with agility and precision, reducing the drag despite its heavy mass. This concept of tubercles has been adapted to design the wind turbines of airplanes, submarines, and windmills for smoother transport and better efficiency.
Robots with mechanical motor based arms are not suitable for gripping fragile objects as the action of gripping itself could potentially damage the specimen. Hence, in the recent years, soft actuators are developed which are revolutionizing the field of robotics. Moreover, motor based actuators (an actuator is a device that causes a machine or any other device to operate) are being replaced by smart actuators that respond to specific stimuli. Smart actuators include light/heat responsive liquid crystal polymers, solvent/vapor-responsive hydrogels, and heat-responsive shape memory alloys. Some of these smart actuators are inspired by Nature and mimic the biological functions including the blooming of flowers, motion of caterpillars, trapping of flies by Venus flytrap, and the proboscis of butterflies.
In the present study conducted by Mr. Akhil R. Peeketi, Prof. Narasimhan Swaminathan, and Prof. Ratna K. Annabattula from the Center for Responsive Soft Matter, Department of Mechanical Engineering, Indian Institute of Technology (IIT) Madras, Chennai, India and, Dr. Jeroen A. H. P. Sol, Prof. Albert P. H. J. Schenning, and Prof. Michael G. Debije from the Laboratory of Stimuli-Responsive Functional Materials and Devices (SFD), Department of Chemical Engineering and Chemistry, Eindhoven University of Technology (TU/e), Eindhoven, The Netherlands, a soft actuator capable of morphing from a flat film to a cone is developed inspired by the blooming of a Calla Lily flower. The speciality of Calla Lily is that it only has a single petal that blooms from a conical tube to a wider petal. In order to achieve such a complex deformation, a liquid crystal polymer network (LCN) was designed with splay alignment and tapered thickness, both, oriented at 45 degrees to one of the edges of the film. Finite element simulations were performed to optimize the alignment and taper orientations for forming a cone. Lastly, a tapered LCN is fabricated with the optimized design that actually morphed from a flat shape at 40 °C to a conical tube at 90 °C. The results of this study could find application in the development of conical micro jets and soft-grippers.
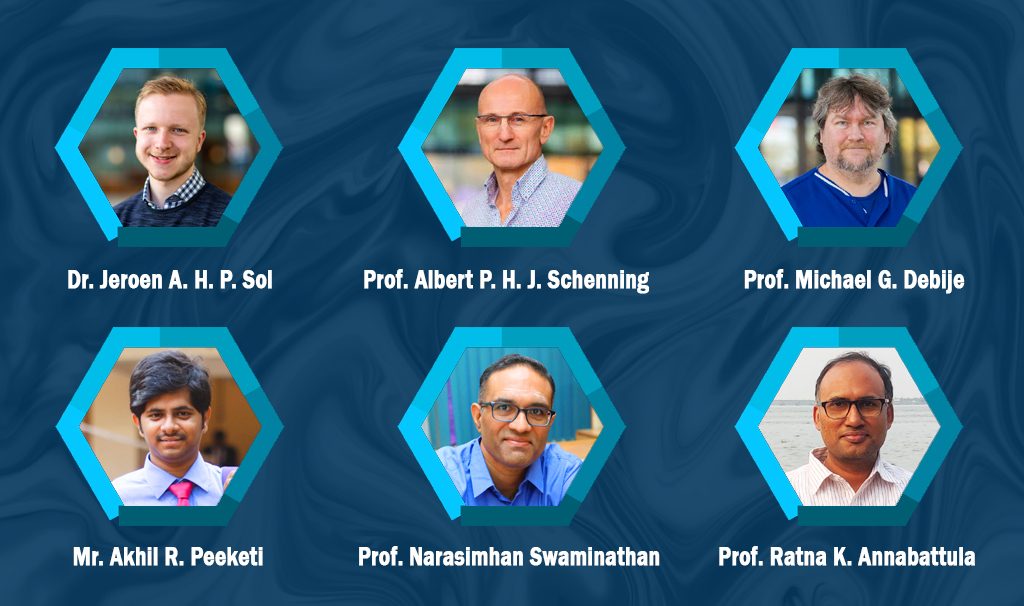
Dr. Sumit Basu, a Professor from Computational Mechanics Group, Indian Institute of Technology (IIT) Kanpur, Kanpur, India, analyzed and appreciated the work done by the authors with the following comments: “Ultra-flexible structures and ultra-soft materials are increasingly being incorporated into engineering designs to create wearable devices, shape morphing structures and soft robots. Among the large number of candidate materials, liquid crystal polymers hold immense promise as they can be chemically `tailored’ to fold and curl up into complex shapes in response to external stimuli like a change in temperature — reminiscent of ways in which flower petals open up in Nature.
The polymer chemistry behind liquid crystal polymers is intricate. The authors have chosen a suitable monomer with ends that are reactive, along with another crosslinker that can actually react with it when exposed to ultraviolet radiation. The crosslinkers link the monomers up to form a ladder-like networked structure at the microscopic scale. Moreover, the entire set of cascading reactions are carefully devised to produce a network that has the monomers aligned in a manner that is tailored through ingenuous photochemistry. The result is a flexible paper-like sheet of a liquid crystal polymer which is deliberately imparted a `taper’. This means that the films are about 1/20th of a millimeter thick at one end and gradually thin down to about 1/50th at another. Added to this is the fact that clever control of the photochemistry causes the monomers to align in a gradually varying and, again, pre-designed, manner. In the present case, the monomers start from being roughly parallel to the bottom surface, gradually change their alignment direction through the thickness and end up being perpendicular to the top surface. The clever combination of taper and varying molecular alignment through the thickness imparts unique mechanical properties to the thin liquid crystal film.
The authors have built a computer model that captures the essential behaviour of the tailored material. Most importantly, mechanical stiffness varies through the thickness in tandem with the variation in molecular alignment and — as is usual for liquid crystalline materials — the material expands anisotropically when heated.
The computer model is encouragingly faithful to the experiments. Utilising the interplay between microscopic molecular alignment and macroscopic tapering patterns, the computer simulations demonstrate that a flat film, on heating, can spontaneously curl up into a variety of shapes — from cylinders to cones.”
Article by Akshay Anantharaman
Click here for the original link to the paper