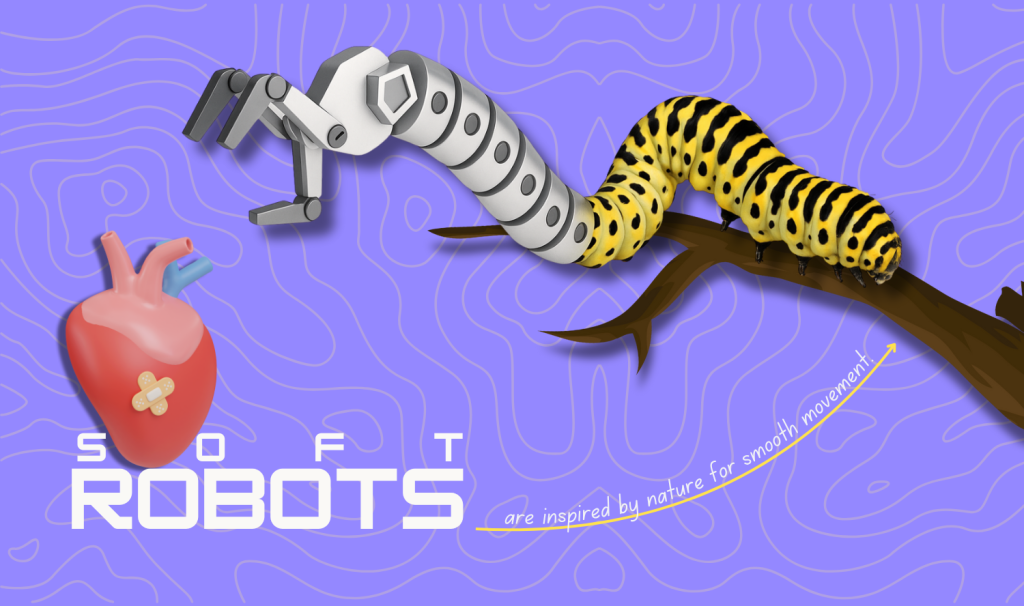
Soft robots are gaining more interest from researchers because of their advantages over rigid-bodied robots. Because soft robots are non-invasive, flexible, and do not cause damage, they find use in the bio-medical field such as in drug delivery and even in surgery.
Soft robots also have the advantage of having locomotion and shape-morphing capabilities. Because of this special quality, they can be made to mimic nature, such as, to jump like a kangaroo, swim like a jellyfish, grip like a Venus flytrap, etc.
In both natural and artificial systems, actuation is governed by external stimuli. While biological organisms respond to factors like light, temperature, and humidity, soft robots can be stimulated by heat, electric fields, light, and magnetic fields.
Of all these stimuli, magnetic stimulation is the most popular because of its remote controllability, fast response, non-harmful nature towards biological materials, and precise control over actuation.
Soft magnetic robots are fabricated by incorporating magnetic particles in a soft polymer matrix. The magnetic particles endow magnetic properties to the soft polymer matrix, allowing it to actuate in the magnetic field.
The magnetic particles can be either hard or soft magnetic particles. The shape morphology for hard magnetic particles is because of dipole interaction, while for soft magnetic particles, it is because of the magnetostriction property of the material.
Hard magnetic particles exhibit a large hysteresis loop, leading to nonlinearities between the applied magnetic field and magnetization. This nonlinearity complicates the establishment of a predictable relationship between the deformation of soft robots and the external magnetic field. In contrast, soft magnetic particles, with their small hysteresis loop and reversible magnetization, enable more linear, controllable, and adaptive shape transformations. Thus, soft magnetic particles are preferred.
In this study, the authors Mr. Dharmi Chand and Prof. M. S. Sivakumar from the Department of Applied Mechanics and Biomedical Engineering, Indian Institute of Technology (IIT) Madras, Chennai, India, have focused on the locomoting motion of an inchworm and the gripping motion of a flower as seen below:
Figure 1 (a) Movement of Inchworm (image courtesy: https://www.allthingsnature.org/what-are-inchworms.htm). (b) Opening of flowers with long petals (image courtesy: https://www.gardenersworld.com/how-to/grow-plants/how-to-grow-cosmos/)
The shape transformation of the soft robot is driven by the orientation configuration of micro-Carbonyl Iron (CI) particle chains, which define the programmed deformation. These particle chains form when the mould with uncured material is exposed to a magnetic field following the mould shape. The configuration pattern of CI particle chains in programmed shape is analysed and then mimicked using thin iron needles/rods with a high aspect ratio in a silicon matrix.
In this study, a soft gripper and a soft locomoting robot were achieved successfully. The performance of the locomotor and gripper was found to be promising and could have potential applications in the medical and robotics fields.
Prof. Bishakh Bhattacharya, HAG Professor from the Department of Mechanical Engineering, Indian Institute of Technology (IIT) Kanpur, Kanpur, India, gave his analysis of the work done by the authors, and pointed out the positives of this work with the following comments: “In this outstanding novel concept, the authors have utilized the magnetostrictive property of iron-powder to create active strain with the help of magnetic stimulation. The active strain can be programmed in order to create different shapes. The concept has been demonstrated for an inch-worm robot and for a gripper configuration. Similar changes, by using traditional smart actuator could be generated through Shape Memory Alloy; however, it works quite slow in comparison to the proposed actuator. Also, due to the absence of significant stress induced phase change, the proposed system is simpler yet can work for a large number of cycle. The proposed technique could also be used to build smart modular robots with pre-programmable shapes. I would look for an elaborate design process to develop such systems in near-future.”
Article by Akshay Anantharaman
Click here for the original link to the paper