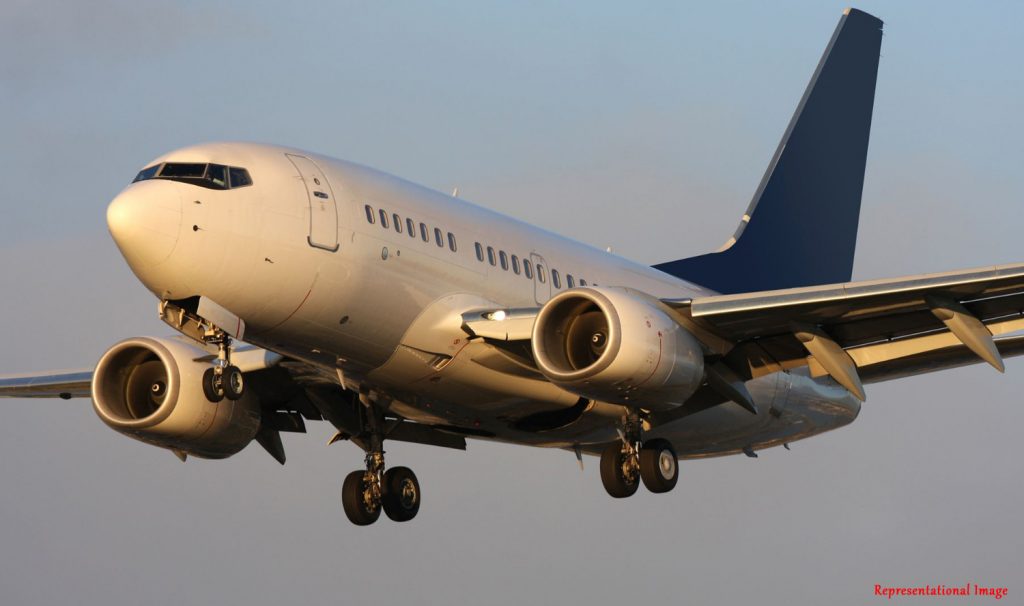
Technologically, we’ve come a long way -during the past four to five decades. The gadgets and technologies we have at our disposal today, in 2025, would seem like something right out of a science fiction to a person 50 years ago.
One of these technologies is 3D printing, otherwise known as additive manufacturing (AM). Additive manufacturing is a process by which a 3D object is created from a CAD (Computer-aided design) model. Typically, materials such as plastics, metals, and ceramics in granular form, are fused to create a fully-formed object. 3D printing was developed in 1986 using stereolithography, and the first commercial 3D printer, SLA-1, was released in 1988 by the 3D Systems Corporation. Today, AM is an up-and-coming component production route suited to applications where small numbers and high functionality are paramount, for example, in the aerospace and medical devices fields. In aerospace, complex part design, reduced wastage and product development cost reduction, are benefits envisioned using AM over traditional manufacturing.
Of the different metals and alloys used in commercial aircraft applications, nickel-based superalloys typically constitute half the total weight of an aircraft engine, highlighting their critical role in withstanding extreme thermal and mechanical stresses at high temperatures. Inconel 718 (IN718) is a nickel-based superalloy that is recognized for its superior properties, including its excellent “creep” resistance (“creep” is a time-dependent plastic deformation mode that prevails at high temperatures), making it a preferred choice for manufacturing aero-engine and rocket engine components. However, AM IN718 displays inferior creep resistance relative to its wrought counterpart, the underlying reason(s) for which has remained elusive. Researchers at IIT Madras, in a recently published paper, have comprehensively demonstrated not only the source of this problem but also have provided a practical solution to resolve it, thereby providing a viable pathway for potential commercial usage of AM IN718.
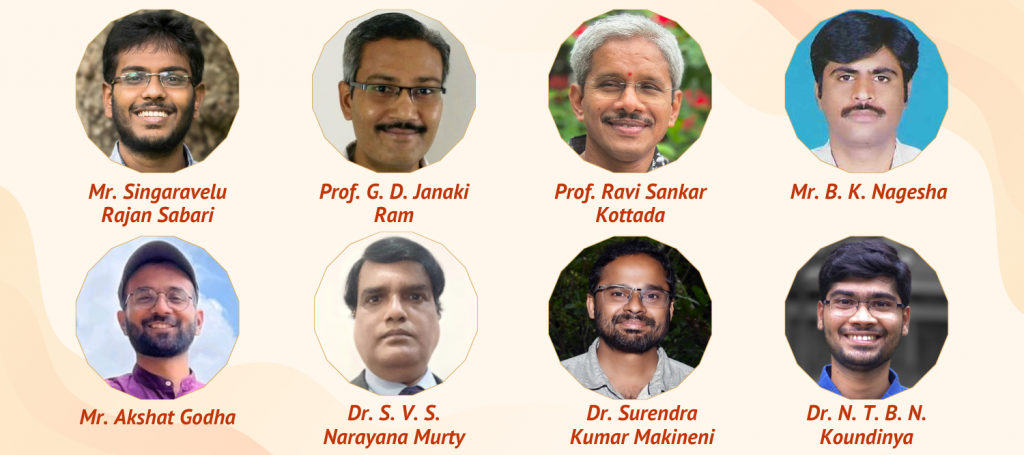
These researchers have unambiguously demonstrated that the less-than-adequate creep resistance of AM IN718 results from the segregation (non-uniform spatial distribution at the microscopic scale) of the element Niobium (Nb) to microstructural features called “grain boundaries” which are inherent in AM-processed materials. Thus, we can think of grains (“single crystals” having a periodic arrangement of atoms in three dimensions) and grain boundaries in “polycrystalline” materials (at the microscopic scale) being analogous to multiple individual tiles being glued together contiguously and making up the macroscopic entity. The consequence of this Nb segregation to the grain boundaries is the formation of Nb-depleted regions adjacent to these grain boundaries called precipitate-free zones (PFZ). These PFZs are relatively soft regions compared to the grain interior and are weak links at high temperatures, leading to the inferior creep resistance.
The formation of these PFZs is attributed to characteristics that are intrinsic to the AM processing of highly-alloyed Ni-based superalloys; in conventional processing, the segregation issue is offset by a secondary thermo-mechanical fabrication step (for example, forging) that enables spatial homogenization of the Niobium atoms. However, this is not possible for the AM IN718 net-shape component, and therefore, it retains its segregation profile. It follows that the prescription for the final solid-state thermal processing of conventional IN718 components to optimize their creep properties is inadequate in eliminating these PFZs in the AM IN718 and, hence, the less-than-optimal creep resistance.
To address this issue, the authors enhanced the driving force for uniform chemical distribution by increasing the solution treatment temperature, thereby providing higher thermal energy for Nb diffusion (mechanism for atomic motion). This approach was given careful consideration, given the potential risk for undesirable structural changes (collateral damage) alongside the desired chemical homogenization. Through detailed microstructural investigations, the solution treatment temperature was optimized at 1150 °C, resulting in improved chemical homogeneity and the elimination of the PFZs. This modification significantly enhanced the creep rupture life, achieving a five-fold improvement compared to the conventional heat treatment.
The authors of this paper and their affiliations are:
- Mr. Singaravelu Rajan Sabari from the Department of Metallurgical and Materials Engineering, Indian Institute of Technology (IIT) Madras, Chennai, India.
- Dr. N. T. B. N. Koundinya from the Department of Metallurgical and Materials Engineering, Indian Institute of Technology (IIT) Jodhpur, Jodhpur, India. Dr Koundinya was also affiliated with the Department of Metallurgical and Materials Engineering, Indian Institute of Technology (IIT) Madras, Chennai, India, and with Max-Planck-Institut für Nachhaltige Materialien GmbH (Max Planck Institute for Sustainable Materials GmbH), Max-Planck-Straβe 1, Düsseldorf, Germany.
- Mr. Akshat Godha from the Department of Materials Engineering, Indian Institute of Science (IISc), Bengaluru, India.
- Dr. Surendra Kumar Makineni from the Department of Materials Engineering, Indian Institute of Science (IISc), Bengaluru, India.
- Dr. S. V. S. Narayana Murty from the Materials and Manufacturing Entity, Liquid Propulsion Systems Centre (LPSC), ISRO, Trivandrum, India.
- Mr. B. K. Nagesha from the Mechanical Engineering Research Facility, Gas Turbine Research Establishment (GTRE), DRDO, Bengaluru, India.
- Prof. G. D. Janaki Ram from the Department of Materials Science and Metallurgical Engineering, Indian Institute of Technology (IIT) Hyderabad, Kandi, India.
- Prof. Ravi Sankar Kottada from the Department of Metallurgical and Materials Engineering, Indian Institute of Technology (IIT) Madras, Chennai, India.
While commenting on the significance of this research, a renowned scientist with immense expertise on high-temperature materials, Prof. Sharvan Kumar, Professor Emeritus, School of Engineering, Brown University, Providence, Rhode Island, USA, acknowledged the importance of this study with the following appreciative comments: “In this paper, the authors have examined the metallurgical characteristics influencing the high-temperature deformation response of additively manufactured Inconel 718, a nickel-based alloy that is a workhorse in the aircraft engine industry; in doing so, they have isolated fine details, intrinsic to the AM process, that can adversely affect performance. The authors have brought together carefully planned experiments, utilized a full suite of contemporary experimental techniques, and performed thorough metallurgical analyses to elucidate a post-manufacturing heat treatment schedule to enhance the high-temperature deformation characteristics central to engine performance. The work is a significant technical contribution relevant to the high-temperature materials community.”
Article by Akshay Anantharaman
Click here for the original link to the paper